What Are the Different Types of CNC Machining?
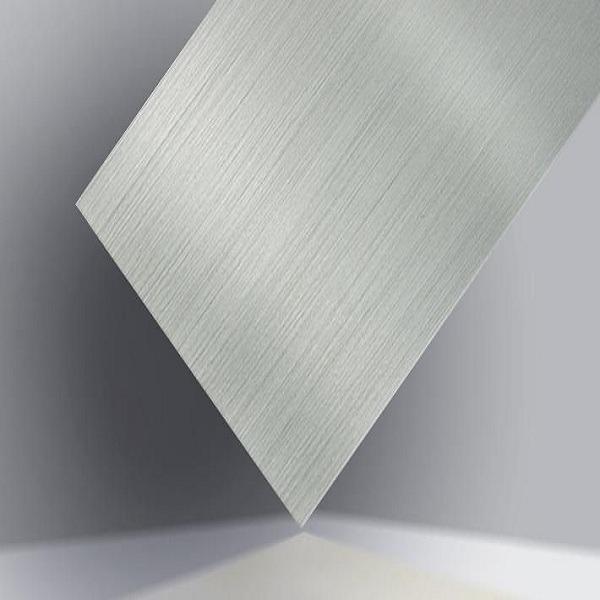
CNC machining encompasses a broad range of techniques, but two main categories dominate the process: Milling and Turning. Each offers distinct functionalities:
CNC Milling
In milling, a rotating cutting tool removes material from a stationary workpiece. This versatility allows milling machines to move the tool along multiple axes (X, Y, and Z) to create intricate 3D shapes. Here are some common milling techniques:
l 3-Axis Milling: This basic form uses three linear axes (X, Y, and Z) for the tool movement, suitable for creating flat profiles, pockets, and slots.
l 4-Axis Milling: Introduces a rotary axis (often the A-axis) for the workpiece, allowing machining on multiple sides without repositioning. This is ideal for complex parts with angled features or cylindrical shapes.
l 5-Axis Milling: The most advanced form, incorporating additional rotary axes (like the B-axis) for both the tool and workpiece. This enables machining of highly complex geometries from any angle.
CNC Turning
Turning involves a stationary cutting tool removing material from a rotating workpiece on a spindle. This process excels at creating cylindrical parts with symmetrical features, such as:
l Straight Turning: Produces simple cylindrical shapes like shafts and bushings.
l Taper Turning: Creates parts with a conical shape, gradually increasing or decreasing in diameter.
l Contour Turning: Utilizes a specially shaped tool path to generate more complex profiles on the rotating workpiece.
l CNC Lathe with Live Tooling: Incorporates additional tools mounted on the rotating tool holder, allowing for milling and drilling operations alongside turning on the same machine. This eliminates the need to move the workpiece between machines for features beyond basic cylindrical shapes.
- Art
- Causes
- Crafts
- Dance
- Drinks
- Film
- Fitness
- Food
- Games
- Gardening
- Health
- Home
- Literature
- Music
- Networking
- Other
- Party
- Religion
- Shopping
- Sports
- Theater
- Wellness
