The Five Most Valuable Applications for Carbon Fiber Sheets
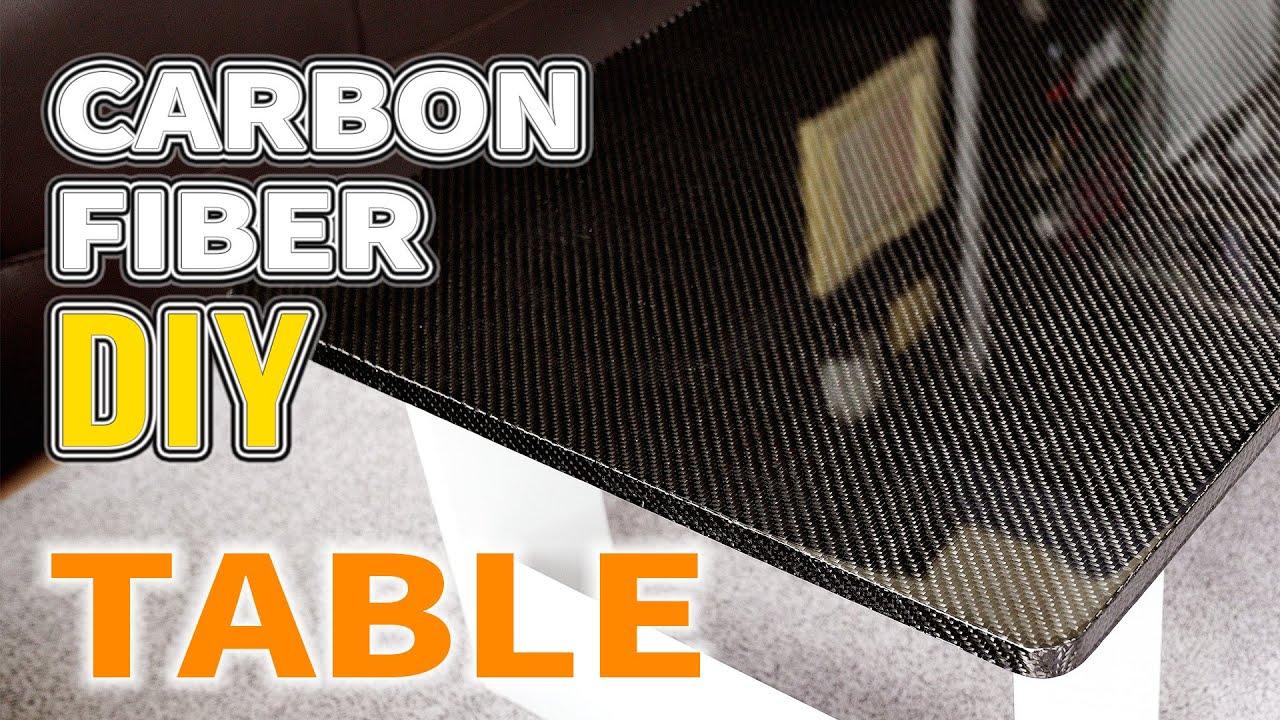
Did you know that carbon fiber has a strength that is five times greater than that of steel? More than 90 percent of the carbon content is made up of carbon fibers. It is primarily recognized for the high tensile strength, the high stiffness, and the low density that it possesses.
Carbon fiber sheets find widespread application in the world of manufacturing thanks to the exceptional strength and density that these sheets possess. It would make an excellent addition to any factory. Therefore, what are some of the applications for carbon fiber that make use of these properties?
Continue reading to find out five of the most important manufacturing applications for carbon fibers.
1. Automotive Applications
Because of their strength and durability, carbon fibers have found a useful application in the automotive industry. Because of this, automotive manufacturers incorporate it into the building of vehicle frames.
Typically found on high-end vehicles like Mercedes-Benz automobiles. For example, replacing unnecessary metal components with carbon fiber can help reduce the overall weight of a vehicle. This results in less consumption of fuel and fewer emissions of carbon dioxide.
The production of vehicles can also be completed more cheaply thanks to carbon fiber. Using alternative materials like aluminum, for example, would drive up production costs significantly.
2. Decoration and Arrangement of Interior Space
Carbon fiber can be used to create a wide variety of new forms and models by designers. Because of this, they are able to create novel and practical ornamental pieces, such as watches.
Because of its durability, it is an excellent choice for the construction of furniture and the implements used in the kitchen.
1. Sheets made of T700 carbon fiber sheet are frequently utilized in the production of picture frames and light fixtures
2. In comparison to the appearance of other materials, this material stands out for its singular appearance
3. It gives rooms a contemporary and futuristic feel without the harshness that metal or glass can bring to a space
3. Sporting Equipment
The sporting equipment of a significant number of professional athletes includes carbon fiber rod and tube sheet. This includes a wide variety of accessories, such as golf clubs, bicycle frames, and bicycle wheels.
Because of its low weight, carbon fiber is increasingly being used in athletic equipment.
- It is more lightweight than wood, plastic, and metal combined
- Athletes will appreciate the convenience this provides when transporting their gear
- As a result, athletes are able to run more quickly and swim further
2015 saw the introduction of tennis racquets that were powered by carbon fiber, making them both faster and stronger.
4. Applications of Carbon Fiber Sheets in the Aerospace Industry
The aerospace industry makes extensive use of carbon fiber in a variety of applications. The year 1940 marks the beginning of the first successful application of carbon fiber in an aircraft. It was the Lockheed Corporation that was responsible for this, as they designed a brand new version of the P-38 fighter plane.
Carbon fiber has played a significant role in recent years in reducing the overall weight of airplanes.
5. Military Equipment
Carbon fiber is used in the manufacturing of high-quality military armor, including ballistic shields and armor. Struts, doors, and cabins are examples of high-strength parts that can benefit from their reinforcement.
It has been used for many years by the Department of Defense (DOD) of the United States. When making weapons out of carbon fiber, such as firearms or knives, the carbon sheet is first shaped into the desired form using a cutting tool. After that, the edges are rounded off so that everything will fit together nicely and remain safe.
At long last, the components are baked at high temperatures in an oven until the curing process is complete. As a consequence of this, finished pieces of equipment are robust despite their low weight, and they are ready for use.
Utilize the Technology Revolving Around Carbon Fiber
To find new and useful applications for carbon fiber sheet, manufacturers and business owners are continuing their research. Rapid advances in technology will make this possible in the near future.
SMI Composites has dedicated itself to the production of cutting-edge composite materials such as carbon fiber. We achieve cost savings through the utilization of autoclave production methods. Therefore, get in touch with us as soon as possible for further details on composite manufacturing.
To make a non-woven material, spread chopped carbon fiber over an uncured layer of 2-part epoxy, then press a sheet of release film on top of that, and finally heat the material to the temperature at which the epoxy will cure. The higher the temperature at which the substance is cured, the more robust it will become. On a plate that had been covered in grease, the epoxy would be spread out.
It will most certainly not have the same cool appearance as carbon fabric embedded in clear epoxy, but it will be considerably more durable.
If you want to make carbon fiber cloth, you can weave the strands together. Chopped strand mat can be made by scattering the chopped fibers in a sheet in a random pattern and coating them with the appropriate binder.
If you want to make a rigid cured sheet, you can either use prepreg or unimpregnated cloth or mat and lay it out within a flat sheet mold with appropriate 2 part polymer - with enough volume to saturate the cloth when catalyzed, most typically epoxy based - and then, once the mold is clamped tight, the part can be bagged and cured under heat and pressure in an autoclave. This method allows you to make a rigid cured sheetNo matter whether prepreg or unimpregnated cloth is used, full strength can only be achieved through the application of heat and pressure.
Because it eliminates the variability that is inherent in hand layup methods, prepreg has a number of benefits, including ease of use, consistency, decreased waste, and maximum achievable strength. In addition to being more expensive, it also has a shelf life, as is the case with all polymer resins because of the nature of the material.
My one and only inquiry would be regarding your reasons for desiring a rigid 3k carbon fiber tube sheet. The cost of is high. If you use standard cloth and the appropriate resin or prepreg, it will cost you significantly more than if you had made the same sheet out of glass fiber cloth or mat and epoxy resins (instead of polyester or vinylester resins). The cost per yard of equivalent glass cloth will be more than double what it would be with standard cloth, and the cost of epoxy resin will be well over five times what it would be with polyester resin. In most cases, it is utilized for structural components that call for high stiffness along with high tensile and compressive strength despite having a low overall weight. Due to its low shear strength as well as its poor resistance to impact and abrasion, it is frequently necessary to protect it with aramid (Kevlar) or another material of a comparable nature.
Because of this, carbon fiber is typically fabricated into structural parts that make use of the material's strengths while mitigating the effects of the material's weaknesses. In these kinds of circumstances, the advantages far outweigh the disadvantages. In addition, keep in mind that in order for it to properly cure, you will need a proper autoclave that is big enough to fit the entire part as well as the molds.
There is nothing wrong with desiring sheet for aesthetic reasons; however, you should be aware that the price will be quite high in comparison to other materials. Especially if you want the finished sheet to be larger without any seams and you don't want to cut it. If the strength properties aren't a concern — for example, if you're just after the look — it is possible to fabricate a large sheet by using cloth as the outer layer, inexpensive glass fiber cloth or mat as the core layers, and using even more T300 carbon fiber cloth as the back layer if the back will be visible. This is possible if you use carbon fiber cloth as the outer layer, inexpensive glass fiber cloth or mat as the core layers, and if the back will be visible. Put everything in place, saturate it with a less expensive resin, and then place it in a vacuum bag so that it can cure at room temperature. This will guarantee that it is completely saturated. You save money while maintaining the same stylish appearance.
- Art
- Causes
- Crafts
- Dance
- Drinks
- Film
- Fitness
- Food
- Giochi
- Gardening
- Health
- Home
- Literature
- Musica
- Networking
- Altre informazioni
- Party
- Religion
- Shopping
- Sports
- Theater
- Wellness
