What Are the Advantages of Powder Coating for CNC Machining?
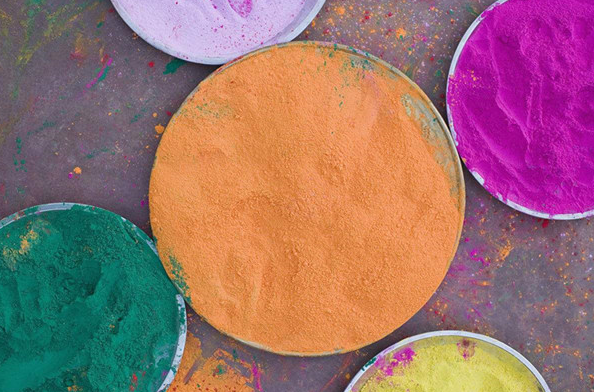
Enhanced Durability:
l Corrosion Resistance: Powder coatings create a robust barrier against moisture, chemicals, and salt, significantly increasing the lifespan of CNC machined parts, especially those operating in harsh environments.
l Abrasion Resistance: They offer superior resistance to scratching, chipping, and wear and tear, crucial for parts subjected to mechanical stress.
l Impact Resistance: Powder coatings can withstand impacts better than many liquid paints, improving the overall durability of the finished product.
Improved Aesthetics:
l Wide Range of Finishes: Available in a vast array of colors, textures (smooth, textured, metallic), and gloss levels, allowing for customization to match specific design requirements.
l Consistent Finish: Powder coating provides a uniform and even coating thickness, resulting in a visually appealing and professional appearance.
Environmental Benefits:
l Reduced Waste: High transfer efficiency minimizes material waste, as overspray can be easily collected and reused.
l No VOCs: Powder coatings are free from volatile organic compounds (VOCs), making them an environmentally friendly alternative to liquid paints.
Cost-Effectiveness:
l Reduced Labor Costs: The powder coating process can be automated, reducing labor requirements and associated costs.
l Increased Efficiency: High transfer efficiency and faster curing times contribute to increased productivity.
Improved Performance:
l Heat Resistance: Many powder coatings can withstand high temperatures, making them suitable for applications in high-temperature environments.
l Chemical Resistance: They offer excellent resistance to various chemicals, making them ideal for use in corrosive environments.
- Art
- Causes
- Crafts
- Dance
- Drinks
- Film
- Fitness
- Food
- Games
- Gardening
- Health
- Home
- Literature
- Music
- Networking
- Other
- Party
- Religion
- Shopping
- Sports
- Theater
- Wellness
