Comparison of T70A Cold Drawn and Hot Rolled Guide Rails
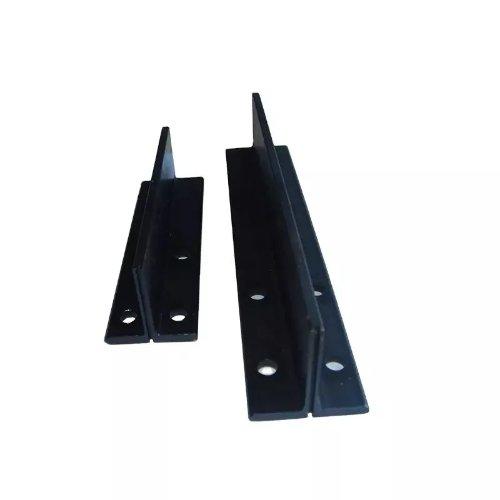
Guide rails are an essential component of various industrial applications, including elevators, cranes, and escalators. They provide stability and guidance to the moving parts and ensure smooth operation. When it comes to selecting guide rails, two popular types that come into consideration are cold drawn and hot rolled T70A guide rails. But which one is better? In this blog post, we'll explore the key differences between these two options and help you choose the best fit for your specific needs. So buckle up as we take a closer look at cold drawn versus hot rolled T70A guide rails!
What are T70A guide rails?
T70A guide rails are a type of steel rail used in various industrial applications to provide support and guidance to moving parts. They are commonly used in elevators, cranes, and escalators. T70A refers to the specific dimensions of the guide rails - they have a height of 70mm and a width of 65mm.These guide rails come in two main types: cold drawn and hot rolled. The manufacturing process for each type differs significantly, resulting in differences in their properties and characteristics.Cold drawn T70A guide rails undergo a manufacturing process that involves pulling or drawing the steel through a die at room temperature. This results in a smoother surface finish with improved dimensional accuracy compared to hot rolled versions.Hot rolled T70A guide rails are made by passing heated steel through rollers at high temperatures. This process makes them less precise than cold drawn versions but results in stronger material due to increased ductility.T70A guide rails offer excellent durability, strength, and stability when utilized correctly. Choosing between cold drawn or hot rolled comes down to your specific application needs.
The difference between cold drawn and hot rolled guide rails
When it comes to guide rails, there are two common methods for manufacturing them: cold drawing and hot rolling. The main difference between these methods is the temperature at which they are processed.Cold drawn guide rails are created by pulling a metal rod through a series of dies at room temperature. This process creates a smooth finish and consistent dimensions, making them ideal for precision applications such as elevator systems or machine tool guideways.On the other hand, hot rolled guide rails are made by heating up the metal and then passing it through rollers while still hot. This method results in a rougher surface finish but can produce longer lengths of rail without any seams or joints.The choice between cold drawn and hot rolled guide rails ultimately depends on your specific application needs. If you require precise measurements and high accuracy, then cold drawn may be the way to go. However, if you need long lengths of continuous rail without any joints or seams, then hot rolled might be more suitable.It's important to consider factors like load capacity, wear resistance, corrosion resistance, and cost when choosing between these two methods. Understanding the differences between cold drawn and hot rolled guide rails can help you make an informed decision that best meets your unique needs.
The benefits of cold drawn guide rails
Cold drawn guide rails have become a popular choice for many applications. These guide rails are produced by pulling the steel through a die at room temperature, resulting in a smooth finish and precise dimensions. Here are some benefits of cold drawn guide rails:
1. Superior surface quality: Cold drawing produces an extremely smooth surface that is free from imperfections such as cracks or tears. This results in less friction between the rail and moving parts, reducing wear and tear.
2. Greater tensile strength: The manufacturing process used for cold drawn guide rails results in higher tensile strength than hot rolled ones. This makes them ideal for use in high-stress applications where durability is crucial.
3. Improved dimensional accuracy: Cold drawing ensures consistent dimensions throughout the entire length of the rail, with minimal deviation from specifications.
4. Cost-effective: Despite their superior properties, cold drawn guide rails are often less expensive than their hot rolled counterparts due to reduced processing time and lower energy consumption during production.If you're looking for a durable, cost-effective solution that offers improved performance over traditional hot rolled guide rails, cold drawn options may be your best bet!
The benefits of hot rolled guide rails
Hot rolled guide rails are manufactured by heating the steel to a high temperature and then rolling it into the desired shape. One of the primary benefits of hot rolled guide rails is their strength. The high temperatures used during production allow for the creation of thicker, stronger rail sections that can withstand more weight and stress than their cold drawn counterparts.Another advantage of hot rolled guide rails is their cost-effectiveness. Because they require fewer manufacturing steps than cold drawn options, hot rolled rails generally have lower production costs. This translates to a lower price point for customers without sacrificing quality or durability.Hot rolled guide rails also offer improved surface finish compared to other types of steel products. This means that they provide better wear resistance, as well as greater resistance against corrosion and rust.Hot rolled guide rails are available in a wider range of sizes and shapes than other types of steel products. This makes them ideal for use in custom applications where specific sizes or shapes may be required.If you're looking for a strong, durable product at an affordable price point with excellent surface finish properties – then hot-rolled guide rail might be just what you need!
How to choose the right guide rail for your application
When it comes to choosing the right guide rail for your application, there are several factors that you need to consider. You should identify the specific requirements of your application and determine what kind of load capacity and precision are needed.Next, think about the operating environment in which your guide rail will be used. Will it be exposed to extreme temperatures or harsh chemicals? This information is important because different materials have varying levels of resistance to these conditions.You should also look at the manufacturing process used for the guide rails you are considering. Cold drawn guide rails offer greater dimensional accuracy and a smoother finish compared with hot rolled ones. On the other hand, hot rolled guide rails tend to be more economical and readily available.Don't forget to take into account any additional features that may improve performance or durability, such as corrosion-resistant coatings or specialized lubricants.By taking all of these factors into consideration when selecting a guide rail for your application, you can ensure optimal performance and longevity from this vital component.
Conclusion
After comparing the features and benefits of cold drawn T70A guide rails versus hot rolled ones, it is clear that each type has its advantages depending on the specific application.
If you require a more precise finish with tighter tolerances, then cold drawn guide rails are the ideal choice. They are also able to handle higher loads and provide smoother movement due to their consistent surface finish.On the other hand, if load capacity is your top priority and you do not require as much precision in your application, then hot rolled guide rails might be a better option for your needs. They are easier to manufacture at larger sizes and can handle heavier loads than cold drawn guide rails.In any case, it's essential to choose a reputable supplier who can provide high-quality materials for your project requirements. The right choice will ensure reliability, longevity and improved overall performance of your mechanical systems.All things considered; both T70A cold-drawn and hot-rolled guide rails have unique qualities that make them suitable for different applications. It's up to you as an engineer or designer to determine which one best fits your specific needs based on cost-effectiveness, tolerance level requirements among others while ensuring they meet safety standards set forth by industry regulations in place.If you need,welcome to contact us.763562759@qq.com
- Art
- Causes
- Crafts
- Dance
- Drinks
- Film
- Fitness
- Food
- Jogos
- Gardening
- Health
- Início
- Literature
- Music
- Networking
- Outro
- Party
- Religion
- Shopping
- Sports
- Theater
- Wellness
