Die castings made of zinc alloys have a problem with shrinking and this issue needs to be addressed
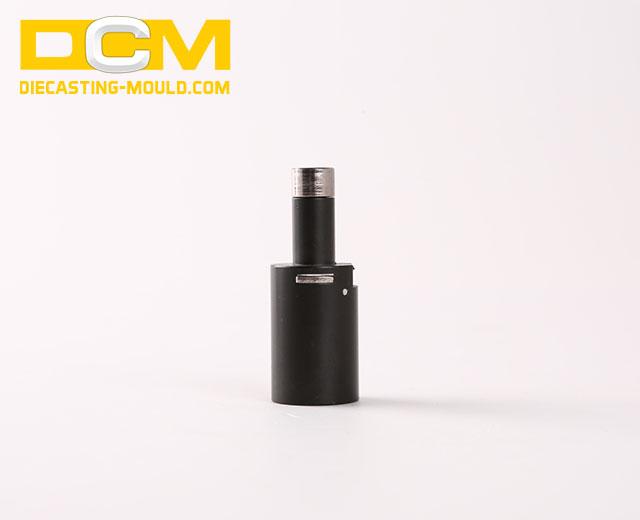
The idea of pressure can be applied to two different contexts when discussing the physical principles involved. The first scenario takes place in a liquid environment and illustrates Archimedes' law in action. In circumstances involving solid states, we die casting products refer to it as the solid-state pressure. If we get the two concepts mixed up, we will run into significant issues.
Only liquid systems are able to make use of the concept of liquid pressure, which has a pressure value that is directional, is a vector pressure, and has a direction that corresponds to the direction in which the feeding force is being applied.
The shrinkage cavity and porosity defects that are common to castings can be effectively solved by adopting the process of filling the mold by die casting first, then forging and shrinking. This is an effective way to solve the aluminum casting factory problems, and it is also an ultimate means. the procedure of making.
This particular kind of die-casting die forging equipment for continuous casting and continuous forging has an appearance that is quite comparable to that of a typical vertical or horizontal die-casting machine. The utmost amount of pressure that can be applied during the forging process. It is possible for the force to be equivalent to the die-casting machine's highest possible clamping force. In the alternative, if we purchase die-casting die forging equipment that has a large clamping force but a small die forging feeding force, the usefulness of the equipment will be significantly diminished.
The blank that is produced by this die-casting die forging machine has an extremely high level of dimensional accuracy and an extremely high level of surface finish, which can be equivalent to the level of precision and surface roughness that can be achieved by machining methods that are above level 6. It is already capable of being categorized as an extreme form of ---The process means that it is one step beyond the process of having no cutting and having a small margin of error. Investigation into the speedy selection of die-casting process parameters for molds used in die-casting, with the conditions being kept constant. On the basis of this information, while actually debugging and producing the product, we can avoid unnecessary detours in the process of setting the parameters of the process, quickly finish debugging the mold, and produce qualified products. The expense of die-casting molds makes up a significant portion of the total cost of die-casting parts, and this expense is factored into the overall price of each die-casting part. life, minimize the cost of die-casting molds' contribution to the overall cost of each die-casting part, and maximize the benefits they provide.
Die castings are characterized by a solidification characteristic known as cooling from the outside to the inside; therefore, if the wall thickness of the casting is relatively high, there will invariably be problems associated with shrinkage on the inside of the casting. Therefore, the problems of shrinkage and porosity are unavoidable and cannot be solved for zinc alloy die castings, particularly thick die castings. This is especially true for thin die castings. What exactly is this approach?When considering shrinkage and porosity defects in castings from the point of view of process principles, the only solution that can be carried out according to the feeding process is to shrink the castings. Castings are subject to a natural physical phenomenon known as phase change shrinkage, which occurs during the solidification process. WeWe can't go against the laws of this natural phenomenon; the only way to solve this problem is to follow the laws of this natural phenomenon. In order for our die-casting process system to achieve natural feeding, the system must have a process that is capable of achieving sequential solidification measures. The intuitive belief that utilizing low-pressure casting methods can solve shrinkage and porosity defects in castings is held by a large number of people; however, this is not the case.
The use of low-pressure casting technology does not guarantee that problems with castings such as shrinkage and porosity will be eliminated. If the system used for the low-pressure casting process does not have feeding process measures, then the blank that is produced using this method of low-pressure casting may always have shrinkage cavities and porosity defects. It's possible that the most fundamental reason is that the sequential solidification process always calls for a relatively long casting time. The die-casting process itself is somewhat at odds with the length of time required for the solidification process. The shortest possible solidification time, which is typically only a quarter or less of that required for sequential solidification, is the most notable characteristic of forced solidification feeding. The first level is the one that can practically eliminate shrinkage cavities and porosity defects in castings, and the second level is the one that can make the interior of the blank reach broken grains or forged structures. Both of these levels are described in more detail below. If you are interested in using,These two distinct degrees are each expressed through a distinct choice of words. The first can be expressed through squeezing and feeding, while the second can be expressed through forging and pressing.
- Art
- Causes
- Crafts
- Dance
- Drinks
- Film
- Fitness
- Food
- Jeux
- Gardening
- Health
- Domicile
- Literature
- Music
- Networking
- Autre
- Party
- Religion
- Shopping
- Sports
- Theater
- Wellness
