Electro nickel plating is the term given to the method that is utilized here
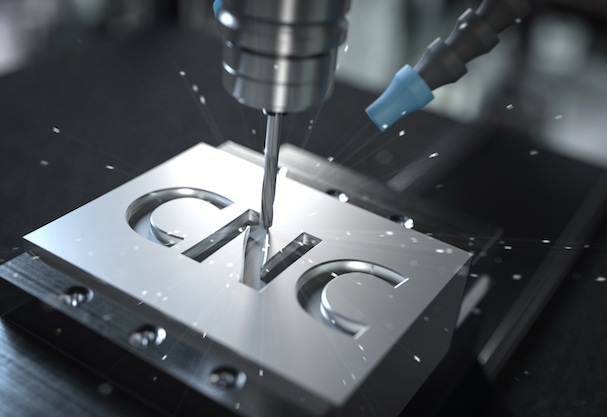
The application of nickel in an electrochemical manner is possible with the help of this plating method. During the process of carrying out this procedure, a direct current will be utilized.
In general, the electroplating process has the potential to improve a wide variety of characteristics CNC machining services are not normally found in the base material. These improvements can be made to a wide variety of different qualities. Electro nickel plating has the potential to improve a product's brightness as well as the product's overall appearance. This is because electro-nickel plating is composed of nickel and nickel oxide. Depending on which nickel-plating chemicals are used during the process, a wide variety of different finishes can be achieved. Matte, pearl, and satin are some of the finishes that are included here, in addition to semi-bright and fully bright cosmetic effects.
The Procedures That Are Involved in the Nickel Electroplating Process
-
A negative charge must first be applied to the base material before nickel can be transferred onto the surface of a product in the appropriate manner
-
This is necessary before nickel can be transferred onto the surface of a product
-
This guarantees that the nickel will adhere in the correct manner
-
After it has been fastened in place, a rod made of nickel is connected to the positive side of the rectifier or the power source in a manner that is analogous to what has been detailed in the prior sections
After the preliminary procedures have been finished, the material that is going to be electroplated is put into a solution that contains a salt that has a chemical composition that includes the electroplating metal. This solution is then allowed to sit for some time. This solution is then allowed to rest for a while before being used. Following that, this solution is put under water. Because the solution contains an electric current, the nickel chloride salt will dissociate into positively charged nickel cat-ions and negatively charged chloride ions. This is because the electric current causes the dissociation. After being attracted to the positively charged nickel rod, the negatively charged chloride anions are then drawn to the negatively charged base metal by the negative charge of the base metal. From this point forward, the oxidized nickel will be drawn to the base material, and it is this base material that will ultimately coat the product.
The CNC machining service of nickel conforms to the description of the current density that is presented in the following passage:
When plating nickel, a wide variety of current densities must be utilized at the various stages of the process to achieve the desired result. To be more precise, the rate at which nickel will be deposited is directly proportional to the current density: the higher it is, the faster it will be deposited. The higher the current density, the faster nickel will be deposited. This is because the optimum level of current density is dependent on both of these factors working together.
The electro-nickel plating procedure should be started as the very first step in the process.
One more method that can be utilized to solve the problem of current density is the addition of a strike layer to the preliminary electro-nickel plating process. This is one of the strategies that can be used. This kind of nickel plating is also known as flash nickel plating, which is another name for it. In certain circumstances, a strike layer may also be referred to as a flash layer or flash nickel plating. These are both alternative names for the same thing. The product has been given a measurement of one micrometer. Striking is a process that can be used when the product's base material needs to be plated with a variety of metals, and it is one of those processes.
Before the application of nickel plating, there are several steps that need to be completed.
Directly responsible for the quality of the electro nickel plating and the rate at which it deposits are the pre-treatment and post-treatment of the base product that is carried out appropriately. The cleaning of surfaces is also possible by utilizing a combination of these methods. Sandblasting and chemical etching are two additional techniques that may also be utilized.
Before beginning the electro-nickel plating process, it is a good idea to test the level of cleanliness present in the base material after the pre-treatment cleaning has been completed but before beginning the process itself. This is done in preparation for starting the electro-nickel plating process. It is important to complete this step before starting the actual process. It is highly recommended that you carry out the waterbreak test to complete this task. Success will depend on your ability to do so. If there are no contaminants on the surface of the base material, such as oils, then a thin layer of water will be able to lie flat and uninterrupted across the entire surface. This will allow the water to form a hydrophobic barrier. Because of this, the water will be able to form a hydrophobic barrier.
- Art
- Causes
- Crafts
- Dance
- Drinks
- Film
- Fitness
- Food
- Jocuri
- Gardening
- Health
- Home
- Literature
- Music
- Networking
- Alte
- Party
- Religion
- Shopping
- Sports
- Theater
- Wellness
