Reliable Leak Detection Tools for Accurate Results
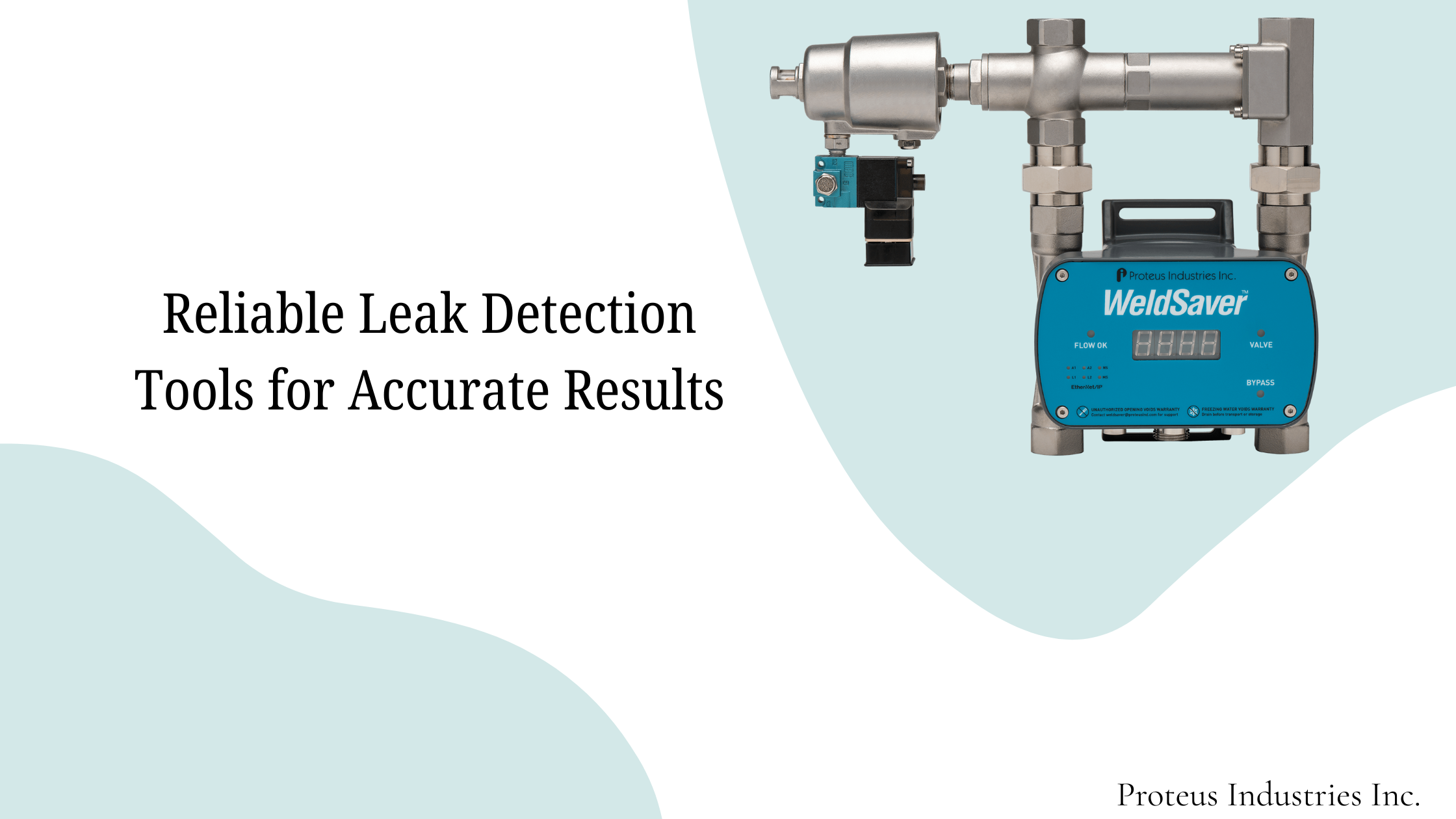
Leak detection is essential in manufacturing, energy, and utility industries, where even the most minor leak can lead to crucial safety hazards, environmental damage, or financial losses. Using the right leak detection equipment in these settings can ensure accurate and reliable results, ultimately improving safety, reducing risks, and optimizing operational efficiency.
This guide delves into the importance of leak detection, the types of equipment available, and how reliable leak detection tools can help achieve accurate results. It also provides insights into the best practices for selecting leak-detection equipment that meets your needs.
Importance of Leak Detection
Leaks in pipes, tanks, or systems can result in unstable situations such as chemical spills, gas leaks, or water damage. Detecting these leaks early is vital in preventing these potential disasters. Industries use leak detection equipment to find and locate leaks before they cause significant harm, leak detection equipment whether it’s resource loss, equipment damage, or the potential for accidents.
Detecting leaks quickly and accurately can save lives and resources in sectors like oil and gas, manufacturing, HVAC systems, and food production. Leak detection systems prevent damage, reduce maintenance costs, and improve operational efficiency. Furthermore, they help organizations comply with safety and environmental regulations by ensuring the safety of workers and preventing contamination or damage to the environment.
Types of Leak Detection Equipment
Several types of leak detection equipment are designed for specific leaks and environments. Depending on the application, the suitable leak detection tools can vary. Here’s an overview of the common types of leak detection equipment used across industries:
Ultrasonic Leak Detectors
Ultrasonic leak detectors typically detect gas, steam, or air leaks in pressurized systems. These detectors listen for the sound of leaks, often inaudible to the human ear, leak detection equipment and convert it into detectable ultrasonic waves. The equipment then identifies and locates the leak based on these ultrasonic signals.
- Advantages: Non-invasive, accurate, and quick.
- Best For: Compressed air, steam, and gas leak detection in industrial settings.
Pressure Decay Leak Testers
Pressure decay testers work by pressurizing the system under test and then monitoring the rate at which the pressure drops. A pressure drop indicates a leak in the system. This type of leak detection equipment is beneficial for detecting small leaks that may not be audible or visible.
- Advantages: Precise measurement and ideal for small leaks.
- Best For: Containers, pipes, and other closed systems.
Tracer Gas Detection
This method uses gases like hydrogen or helium entered into the tested system. The equipment detects the presence of these gases when they escape from a leak, making it easier to locate and pinpoint the source of the leak.
- Advantages: Highly sensitive and effective for detecting tiny leaks.
- Best For: Pipelines, tanks, and vacuum systems.
Infrared Leak Detectors
Infrared detectors are designed to detect gas leaks by analyzing the infrared radiation emitted from gases, including methane and carbon dioxide. When a gas escapes from a system, leak detection equipment absorbs specific infrared wavelengths, which the equipment detects.
- Advantages: Non-contact, can cover large areas quickly.
- Best For: Gas leaks in outdoor environments or hard-to-reach areas.
Helium Leak Detectors
Helium is used as a tracer gas in many applications. Leak detectors using helium measure the concentration of helium that leaks out of a system. This technology is accessible, and even tiny leaks can be detected effectively.
- Advantages: Highly accurate for detecting tiny leaks.
- Best For: Vacuum systems, high-tech manufacturing, and aerospace applications.
Coolant leak Detectors
Coolant leak detectors are crucial in identifying and preventing leaks within industrial coolant systems. These devices offer early detection, helping to avoid costly repairs and downtime. Utilizing advanced technology, such as the WeldSaver from Proteus Industries, they employ high-precision sensors to identify even small leaks. By ensuring the integrity of the coolant system, these detectors help optimize performance, safeguard equipment and reduce the risk of overheating or damage to system components.
How Reliable Leak Detection Tools Ensure Accurate Results
Accurate leak detection is not just about having the right equipment—it's also about using the tools effectively. Reliable leak detection tools are built to give consistent, reproducible results, ensuring that even the smallest leaks are detected and accurately located. Here are some key factors that make leak-detection tools reliable:
- Sensitivity and Precision: Leak detection tools must be sensitive enough to detect even minor leaks. This sensitivity is crucial in industries where even the slightest gas or liquid escape can lead to catastrophic consequences. For example, using tools with high sensitivity ensures that gas leaks in pipelines are detected before they escalate into dangerous situations.
- Speed and Efficiency: Leak detection tools must be able to identify and pinpoint leaks quickly. In industrial settings, minimizing downtime is essential for maintaining productivity. Reliable leak detection equipment can deliver fast results, enabling quick maintenance and repairs, thus preventing long-term disruption.
- Durability and Reliability: Leak detection equipment often operates in harsh environments, so robust and durable tools are essential. Reliable tools can withstand extreme temperatures, pressure, and environmental conditions, making them suitable for various applications, from outdoor gas leak detection to high-pressure systems.
- Non-Invasive Detection: Non-invasive leak detection tools are designed to detect leaks without requiring disassembly or significant intervention. This method allows quick and hassle-free inspections, especially when the system cannot be shut down or disassembled, such as in running pipelines.
Benefits of Using Reliable Leak Detection Equipment
Investing in high-quality leak detection equipment brings numerous benefits to an organization, including:
- Improved Safety: The primary benefit of using reliable leak detection tools is enhanced safety. Detecting leaks early prevents accidents such as explosions, fires, and toxic gas exposure. Safety is critical in dangerous environments like chemical plants or natural gas pipelines, and effective leak detection is a necessary preventive measure.
- Cost Savings: Detecting leaks early helps prevent damage to expensive equipment, machinery, and infrastructure. Small, undetected leaks can lead to system failure, resulting in costly repairs. Organizations can avoid the high costs associated with large-scale damage and downtime by identifying leaks in their early stages.
- Environmental Protection: Leaks can have severe ecological impacts, especially in industries that handle chemicals, fuels, or gases. Detecting and repairing leaks helps organizations comply with environmental regulations and avoid fines or environmental disasters such as contamination or spills.
- Increased Operational Efficiency: Reliable leak detection ensures systems run at peak efficiency. Unnoticed leaks lead to energy losses or wasted resources, directly impacting productivity. By detecting and fixing leaks promptly, organizations can maintain consistent performance and avoid unexpected operational disruptions.
Best Practices for Leak Detection
To ensure the highest efficiency and reliability in your operations, following best practices when using leak detection equipment is essential. Begin with conducting regular inspections, as leak detection should be a continuous process rather than a one-time task. Routine checks, particularly for critical infrastructure, help identify issues early before they escalate into costly repairs or system failures. Equally important is proper training; operators must be thoroughly educated on using the equipment and understand its capabilities and limitations to ensure precise assessments and efficient usage. Furthermore, maintaining your leak detection tools is crucial. These instruments should be calibrated frequently and kept in good working condition to maintain sensitivity and accuracy. Without regular maintenance, the effectiveness of even the most advanced tools can degrade, leading to missed detections or false readings. By incorporating these best practices, businesses can maximize their leak detection efforts, enhance safety, reduce downtime, and maintain operational integrity.
Conclusion
Reliable leak detection tools are indispensable for industries that deal with hazardous materials, high-pressure systems, or large-scale infrastructure. Using the right equipment ensures that leaks are detected early, reducing the risk of accidents, environmental damage, and operational inefficiencies. With the advancement in leak detection technology, leak detection equipment tools like ultrasonic detectors, pressure decay testers, and tracer gas methods provide more accurate and efficient ways to detect leaks.
When selecting leak detection equipment, it is essential to consider the tools' sensitivity, speed, and durability to ensure reliable results. Investing in quality leak detection equipment improves safety, saves money, protects the environment, and enhances overall operational efficiency.
For more information on effective leak detection solutions, visit Proteus Industries’ WeldSaver Overview.
FAQs
What is the most reliable method for leak detection? The most reliable method depends on the type of leak. Ultrasonic and pressure decay testers are among the most popular and reliable for general industrial use.
How often should leak detection be performed? Leak detection should be performed regularly, especially for systems handling hazardous materials. For high-risk systems, it is recommended that inspections be conducted annually or even more frequently.
Can leak detection equipment be used in all environments? Yes, most modern leak detection tools are scheduled to operate in various environments, including extreme temperatures and pressures.
What should I do if my leak detection equipment detects a leak? Once a leak is detected, the system should be shut down immediately if necessary, and repairs should be performed as soon as possible to prevent further damage or hazards.
How do I know which leak detection equipment to choose? Choose equipment based on the type of leak, the environment, and the level of sensitivity required. Consulting with an expert or reviewing manufacturer recommendations can help determine the best option.
- Art
- Causes
- Crafts
- Dance
- Drinks
- Film
- Fitness
- Food
- Spellen
- Gardening
- Health
- Home
- Literature
- Music
- Networking
- Other
- Party
- Religion
- Shopping
- Sports
- Theater
- Wellness
