Precision Unleashed: The Triad of Molds Transforming Cap Production
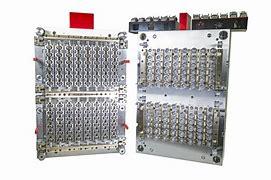
In the dynamic realm of molding technology, three distinct players have emerged to revolutionize the production of slitting caps. The slitting cap mould, cavity slitting mould, and sliding cap mould collectively represent a trinity of innovation, transforming the manufacturing landscape with their precision engineering. This article delves into the intricacies of each mold type, exploring their important features, applications, and the collective impact they've had on various industries.
Understanding the Trifecta: Slitting Cap Mould, Cavity Slitting Mould, and Sliding Cap Mould
1. Slitting Cap Mould: Precision in Simplicity
The slitting cap mould serves as the foundational force behind the production of slitting caps. Its design emphasizes simplicity while maintaining a high degree of precision. This mould type is adept at creating uniform slits in caps, a important feature for various applications in industries such as packaging and beverage.
2. Cavity Slitting Mould: Elevating Complexity for Efficiency
The cavity slitting mould takes precision a step further by incorporating multiple cavities within a single mold. This ingenious design allows for the simultaneous creation of multiple slitting caps in each molding cycle, significantly enhancing production efficiency. Industries with high-volume demands find the cavity slitting mould particularly advantageous.
3. Sliding Cap Mould: Dynamic Adaptability for Varied Designs
The sliding cap mould introduces a dynamic element to the slitting cap production process. With its important sliding mechanism, this mould accommodates designs that require intricate or asymmetrical slitting patterns. This adaptability makes the sliding cap mould a versatile solution for industries with diverse cap design requirements.
Features and Mechanisms
1. Slitting Cap Mould:
The slitting cap mould typically consists of a single cavity with precision-cutting features. It leverages a straightforward yet effective mechanism to create clean and uniform slits in caps. This design is well-suited for applications where simplicity and precision are paramount.
2. Cavity Slitting Mould:
The cavity slitting mould features multiple cavities arranged strategically to optimize the use of space and maximize production output. The mechanism involves synchronized movements that allow for the simultaneous creation of slits in multiple caps. This design is characterized by its efficiency and scalability.
3. Sliding Cap Mould:
The sliding cap mould introduces a sliding mechanism to the traditional molding process. This mechanism allows for intricate movements during the molding cycle, enabling the creation of caps with dynamic and non-uniform slitting patterns. The sliding cap mould is ideal for applications that demand important and customized cap designs.
Applications Across Industries
1. Packaging Industry:
In the packaging industry, slitting caps are integral components for various products, from beverages to pharmaceuticals. The slitting cap mould, with its precision and simplicity, caters to the high demand for uniform slitting in caps. The cavity slitting mould excels in high-volume production, while the sliding cap mould adds versatility for customized packaging solutions.
2. Beverage Manufacturing:
The beverage industry relies on efficient production processes to meet consumer demands. The slitting cap mould ensures that caps for beverage containers are precisely slit, facilitating easy access to the contents. The cavity slitting mould enhances productivity, while the sliding cap mould allows for innovative and eye-catching cap designs.
3. Pharmaceutical Packaging:
Pharmaceutical products often require specialized packaging solutions. The slitting cap mould contributes to the creation of caps that ensure the integrity and safety of pharmaceuticals. The cavity slitting mould meets the demands of large-scale pharmaceutical production, while the sliding cap mould accommodates important requirements for specific medications.
4. Customized Cap Designs:
Industries that prioritize important and customized cap designs, such as cosmetics or premium consumer goods, benefit from the versatility of the sliding cap mould. This mould type allows for the creation of caps with intricate slitting patterns, adding aesthetic value to the final product.
Advantages and Innovations
1. Efficiency and Speed:
The slitting cap mould, with its simplicity, offers an efficient and speedy solution for precision slitting. The cavity slitting mould takes efficiency to the next level by enabling the simultaneous production of multiple caps. The sliding cap mould, while slightly more intricate, maintains efficiency and adapts to varied design requirements.
2. Scalability for High Volume Production:
The cavity slitting mould is a game-changer for industries with high-volume production needs. Its multiple cavities allow for the creation of numerous slitting caps in a single cycle, reducing production time and costs. This scalability is important for meeting the demands of large-scale manufacturing operations.
3. Customization and Design Flexibility:
The sliding cap mould introduces a new dimension of design flexibility. Its sliding mechanism allows for the creation of caps with important and intricate slitting patterns. This customization is invaluable for industries that prioritize branding and visual appeal in their products.
4. Precision for Quality Assurance:
Across all three mould types, precision remains a common advantage. The precision in slitting offered by these molds ensures the quality and functionality of the final caps. This is particularly important in industries where product integrity and safety are non-negotiable, such as pharmaceuticals.
Impact on Manufacturing Processes
1. Streamlined Production Lines:
The adoption of slitting cap moulds has streamlined production lines across industries. The simplicity, efficiency, and scalability offered by these molds contribute to smoother manufacturing processes, reducing bottlenecks and improving overall productivity.
2. Cost-Efficient Manufacturing:
The cavity slitting mould, by enabling high-volume production, contributes to cost-efficient manufacturing. The reduced cycle times and increased output result in lower production costs per unit, offering a competitive edge to manufacturers in price-sensitive markets.
3. Diverse Product Offerings:
The sliding cap mould, with its design flexibility, allows manufacturers to diversify their product offerings. Customized cap designs cater to niche markets and consumer preferences, opening new avenues for product differentiation and market penetration.
In conclusion, the trinity of slitting cap moulds—comprising the slitting cap mould, cavity slitting mould, and sliding cap mould—represents a pinnacle of innovation in the molding industry. These molds have reshaped the way slitting caps are produced, offering precision, efficiency, and versatility across various applications. As manufacturing processes continue to evolve, the impact of these molds on industries such as packaging, beverage, pharmaceuticals, and more is set to grow, providing solutions that align with the dynamic needs of modern production.
- Art
- Causes
- Crafts
- Dance
- Drinks
- Film
- Fitness
- Food
- Oyunlar
- Gardening
- Health
- Home
- Literature
- Music
- Networking
- Other
- Party
- Religion
- Shopping
- Sports
- Theater
- Wellness
