What Is the Surface Finish Achievable With Wire EDM?
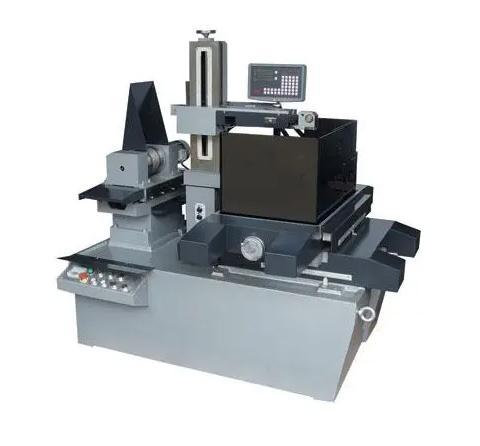
Wire EDM (Electrical Discharge Machining) can produce a wide range of surface finishes, from relatively rough to mirror-like, depending on a variety of factors. This is a detailed breakdown:
Factors affecting surface finish:
l Wire diameter: Thinner wires typically produce finer finishes, but they are limited in terms of material removal rates and cut depths.
l Pulse settings: The peak current, pulse duration, and pulse on time have a direct impact on the rate of material removal and the size of the craters left on the surface. Lower peak currents and pulse durations produce smoother finishes.
l Wire feed rate: Faster wire feed rates produce rougher surfaces because the wire spends less time at each point, resulting in larger craters.
l Flushing conditions: Proper flushing with a dielectric fluid is essential for removing debris and preventing excessive heat buildup, which can contribute to a rougher finish.
l Material properties: The material being cut also plays a part. Harder materials typically require higher peak currents and longer pulse durations, which can result in a rougher finish.
Achievable surface finish ranges:
l Rough: This range usually falls between 25 and 50 Ra (micro inches) and is appropriate for applications where surface finish is not critical.
l Medium: This range is between 10 and 25 Ra and is commonly used for functional parts that require some degree of smoothness.
l Fine: This range runs from 5 to 10 Ra and is used for parts that require a smooth surface finish for functionality or aesthetics.
l Superfine: Wire EDM can achieve a smooth finish of 1-5 Ra, making it ideal for highly polished parts or those with tight tolerances.
While wire EDM can produce extremely smooth finishes, it is important to remember that the process involves melting and vaporizing the material. This results in a thin, resolidified layer called the recast layer on the surface, which may be slightly rougher than the underlying material. Achieving a superfine finish frequently necessitates multiple passes and specialized techniques, which can significantly extend machining time and cost. Polishing or honing may be necessary for critical applications that require extremely smooth surfaces. Wire EDM uses an electrically charged electrode, usually made of graphite or copper, that plunges into the workpiece like a stamp. You might want to learn more about wire EDM, including the differences between wire EDM and Die-Sinking EDM.
- Art
- Causes
- Crafts
- Dance
- Drinks
- Film
- Fitness
- Food
- الألعاب
- Gardening
- Health
- الرئيسية
- Literature
- Music
- Networking
- أخرى
- Party
- Religion
- Shopping
- Sports
- Theater
- Wellness
