What Design Strategies Can Help Reduce CNC Machining Costs for Tolerances and Surface Finishes?
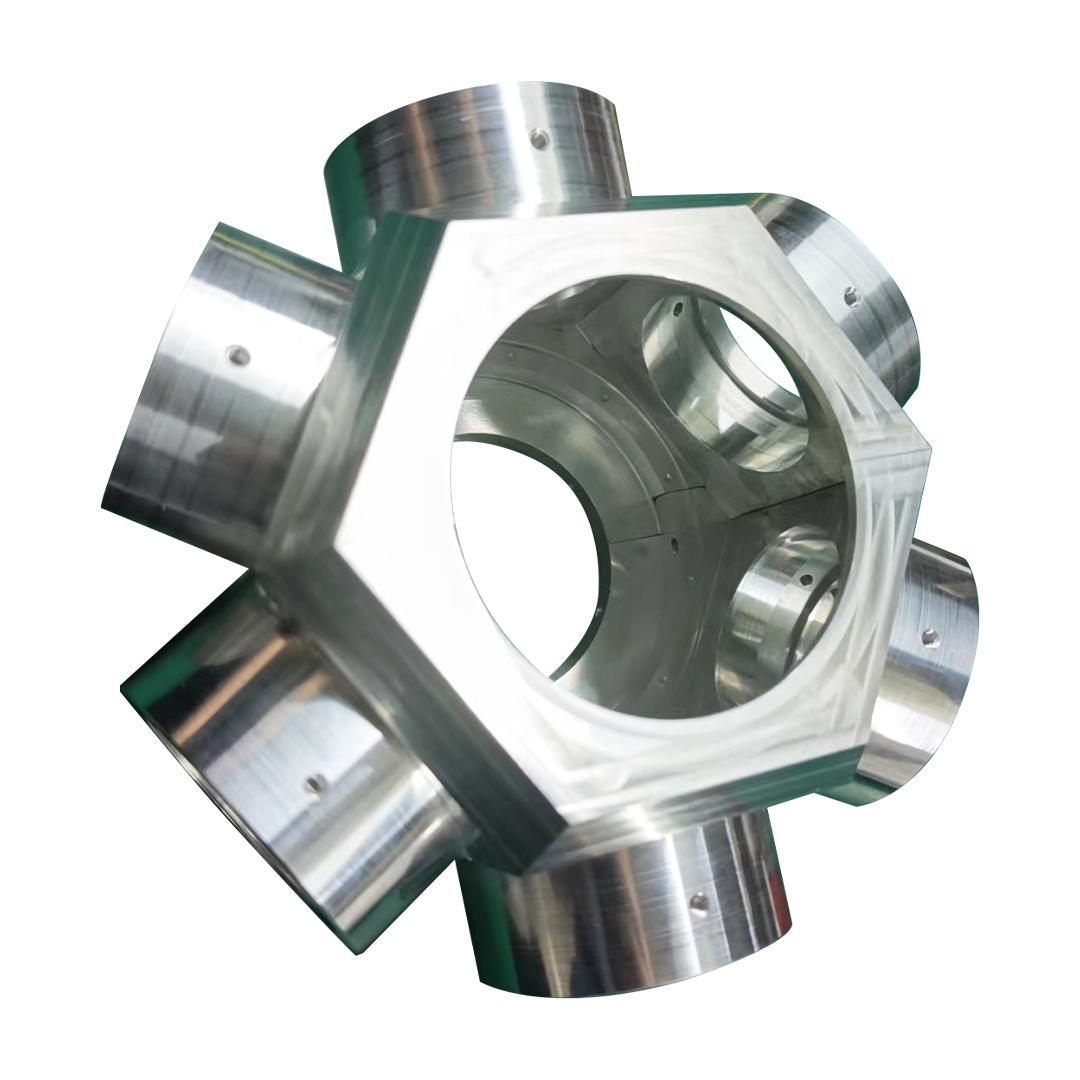
Following Design for Manufacturability (DFM) principles is key to minimizing costs associated with tolerances and surface finishes in CNC machining. Here's a detailed breakdown of design strategies to achieve this:
1. Tolerance Optimization
l Functional Analysis: Analyze how each dimension and feature on your part interacts with other parts in the assembly. Focus on achieving tight tolerances only for critical features that directly affect part movement, fit, or performance. Looser tolerances can be applied to non-critical features like aesthetics or features that don't impact assembly.
l Standardization: Whenever possible, use standard tolerance values (e.g., +/- 0.1mm or +/- 0.005in) across your design. This simplifies manufacturing for CNC shops and reduces setup times, leading to lower costs. Most shops have experience working with these tolerances and can achieve them efficiently.
l Geometric Tolerancing: Use proper geometric dimensioning and tolerancing (GD&T) on your drawings. This clearly communicates your tolerance requirements for specific features like flatness, concentricity, or perpendicularity. Clear GD&T avoids misinterpretations and ensures the CNC shop machines the part to your exact needs.
2. Surface Finish Optimization
l Functional vs. Aesthetic: Define the required surface finish based on functionality, not just aesthetics. A rougher surface finish, like a "machined finish" achieved directly from the cutting tool, is faster and cheaper to achieve than a smoother finish, like a polished finish. Ask yourself if a smoother surface is truly necessary for part performance. For example, a machined finish might be sufficient for a part that will be hidden inside an assembly.
l Minimize Feature Complexity: Features with complex shapes, tight corners, and small radii require slower machining speeds and more tool changes to achieve smooth finishes. This increases cost. Consider simplifying the design by using larger radii, smoother transitions, and eliminating unnecessary details that don't affect functionality.
3. Design for Efficient Machining
l Consolidate Features: Combine multiple features into one whenever possible. This reduces the number of machining operations and tool changes needed to achieve the desired tolerances and finishes. For instance, instead of having separate holes and slots, consider a single cutout that combines both functionalities.
l Minimize Wall Thickness Variations: Large variations in wall thickness within a part can necessitate slower machining speeds and multiple passes to achieve consistent tolerances and surface finishes. Aim for uniform wall thickness whenever possible for efficient machining.
l Minimize Undercuts and Slots: Features like undercuts and narrow slots require specialized tools and can be challenging to machine with tight tolerances and smooth finishes. Redesign the part to minimize or eliminate these features if possible.
4. Utilize Standard Components
l Off-the-Shelf Components: Instead of custom machining specific features, consider incorporating readily available standard components like bearings, fasteners, or spacers. These components often come with precise tolerances and good surface finishes at a lower cost than custom machining them.
5. Leverage Additive Manufacturing (Optional)
l Complex or Intricate Features: For highly complex or intricate features that would be expensive to achieve with CNC machining due to tight tolerances and surface finish requirements, consider using additive manufacturing (3D printing) for those specific features. Then, combine the 3D printed features with simpler CNC machined components for a cost-effective solution.
By implementing these design strategies during the design phase, you can significantly reduce the machining time and cost associated with achieving your desired tolerances and surface finishes in CNC machining. Remember to communicate your design intent and functional requirements clearly with your chosen CNC machining service provider. They can offer valuable insights and suggestions for further optimizing your design for cost-effective manufacturing. For more information please click: A Guide to Cost-Effective Tolerance and Surface Finish Strategies in CNC Machining.
- Art
- Causes
- Crafts
- Dance
- Drinks
- Film
- Fitness
- Food
- Giochi
- Gardening
- Health
- Home
- Literature
- Music
- Networking
- Altre informazioni
- Party
- Religion
- Shopping
- Sports
- Theater
- Wellness
