What Are Some of the Challenges of CNC Milling Aluminum?
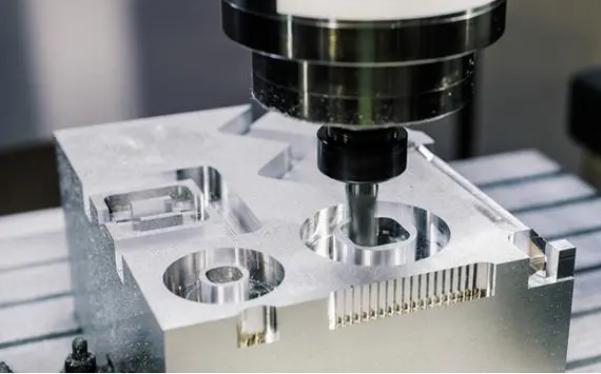
While CNC milling offers numerous benefits for working with aluminum, there are also some challenges to consider:
l Gummy Build-up: Aluminum has a low melting point. If speeds and feeds are not chosen carefully, aluminum can weld or "gum up" the cutting tool. This reduces tool life, affects surface finish, and can lead to tool breakage. Using proper coolant and sharp cutting tools helps mitigate this issue.
l Heat Generation: Friction during the machining process can generate heat. Excessive heat can cause warping or melting of the aluminum workpiece, leading to dimensional inaccuracies and potential scrap. Using proper speeds, feeds, and coolant helps control heat generation.
l Chip Evacuation: The chips produced during aluminum milling can be stringy or "wiry." Improper chip evacuation can lead to re-cutting of chips, which damages the surface finish and reduces tool life. Choosing the right tool geometry and using appropriate coolant helps ensure proper chip evacuation.
l Choosing the Right Alloy and Tooling: With various aluminum alloys available, selecting the right one for your application is crucial. Each alloy has different machining characteristics. Similarly, choosing the appropriate cutting tool material and geometry is essential for optimal results and avoiding challenges like gummy build-up or rapid tool wear.
By understanding these benefits and challenges, you can make informed decisions when choosing CNC milling for your aluminum projects. Careful planning, tool selection, and proper machining practices help ensure successful and efficient aluminum fabrication using CNC milling.
- Art
- Causes
- Crafts
- Dance
- Drinks
- Film
- Fitness
- Food
- Oyunlar
- Gardening
- Health
- Home
- Literature
- Music
- Networking
- Other
- Party
- Religion
- Shopping
- Sports
- Theater
- Wellness
