Exploring the Versatile Applications of Vacuum Form Plastic Sheets
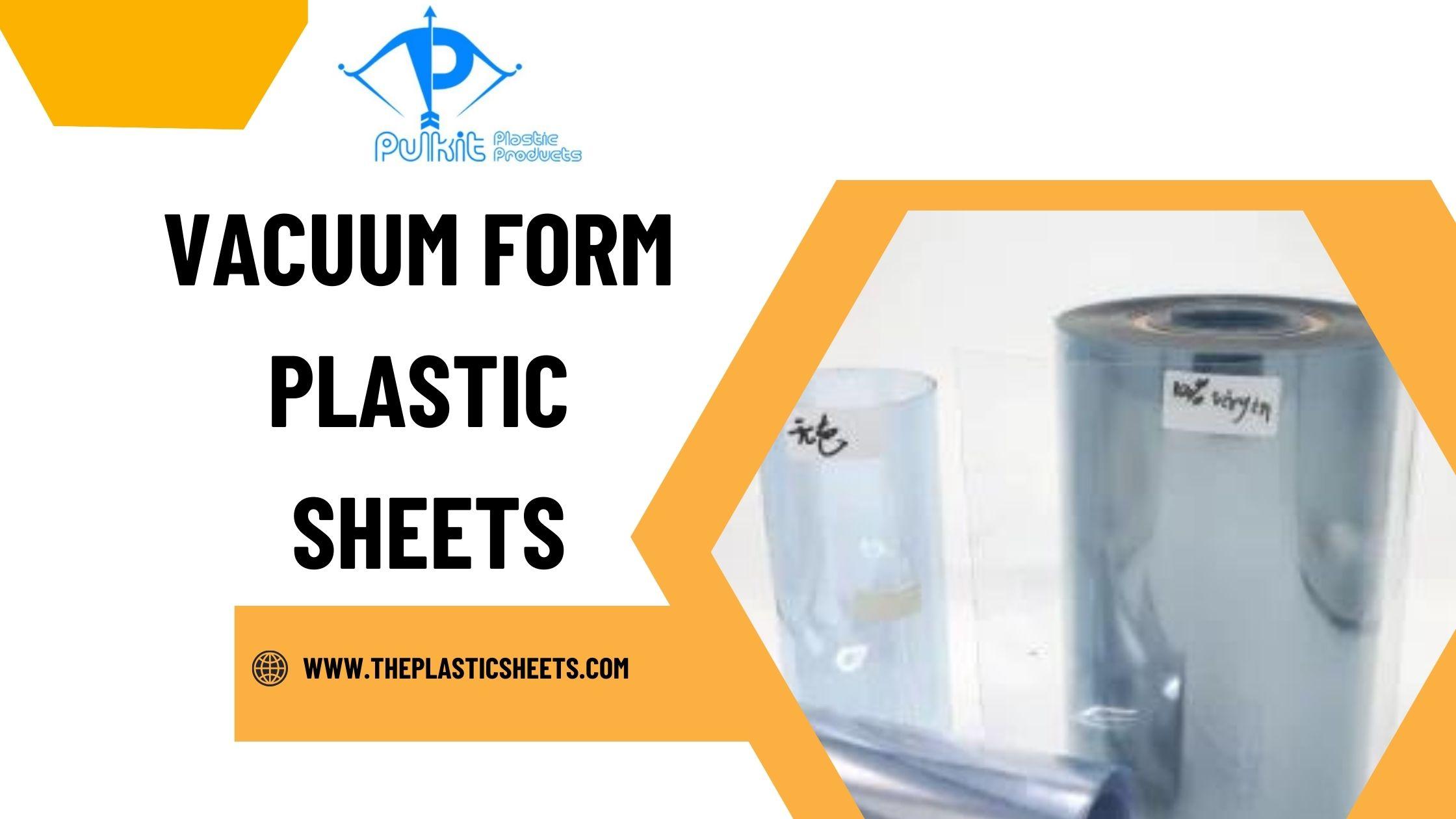
Vacuum form plastic sheets have become increasingly popular in various industries due to their versatility, durability, and cost-effectiveness. This manufacturing process allows for the shaping of plastic sheets into intricate designs and forms, catering to a multitude of applications. In this article, we will explore the various uses of vacuum form plastic sheets, the advantages they offer, and how to choose the right suppliers, including prominent names like Pulkit Plastic Products.
What are Vacuum Form Plastic Sheets?
Vacuum forming is a manufacturing process that involves heating a thermoplastic sheet until it becomes pliable, then using a vacuum to shape it over a mold. This technique is particularly popular for creating three-dimensional objects from flat sheets of plastic. The result is a lightweight, sturdy product that can be used across numerous applications.
Types of Materials Used
Common materials used for vacuum forming include:
- Acrylic: Known for its clarity and resistance to UV light.
- Polycarbonate: Offers high impact resistance, making it ideal for protective applications.
- Polystyrene: Cost-effective and easy to mold, often used in packaging.
- ABS (Acrylonitrile Butadiene Styrene): Durable and resistant to heat, suitable for automotive and consumer products.
Versatile Applications of Vacuum Form Plastic Sheets
1. Packaging Solutions
One of the most common applications of vacuum form plastic sheets is in packaging. Their ability to create custom shapes makes them ideal for packaging delicate items like electronics, glassware, and food products. Vacuum-formed packaging not only protects the product but also enhances its presentation, making it more appealing to consumers.
2. Automotive Components
The automotive industry utilizes vacuum-formed plastic sheets for various components, such as dashboards, door panels, and interior trims. These parts are lightweight yet durable, contributing to improved fuel efficiency without sacrificing performance. Additionally, vacuum forming allows for intricate designs and textures that enhance the vehicle's aesthetic appeal.
3. Medical Equipment
In the medical field, Vacuform Plastic Sheets are essential for creating custom trays, housings, and containers for medical devices. Their ability to be molded into specific shapes ensures that medical equipment is safely stored and transported, minimizing the risk of damage. Moreover, many vacuum-formed plastics can be sterilized, making them suitable for direct contact with medical instruments.
4. Consumer Products
From packaging to parts for toys, vacuum form plastic sheets are widely used in consumer goods. The versatility of the material allows for creative designs that attract customers. Items like food containers, cosmetic packaging, and even custom promotional displays benefit from the unique characteristics of vacuum-formed plastics.
5. Display and Signage
Retail environments often rely on vacuum form plastic sheets for creating eye-catching displays and signage. The ability to mold plastic into various shapes and sizes enables retailers to produce customized promotional displays that stand out. The lightweight nature of vacuum-formed signs also makes installation and transportation easier.
6. Prototyping
Vacuum forming is a cost-effective solution for prototyping. Designers can quickly create prototypes of products to test functionality and aesthetics before moving on to mass production. This iterative process can significantly speed up product development and reduce costs.
7. Industrial Applications
In industrial settings, vacuum-formed plastic sheets are used for creating machine guards, enclosures, and components that require specific dimensions and durability. Their resilience to chemicals and impact makes them ideal for harsh working environments.
Advantages of Vacuum Form Plastic Sheets
- Customization: One of the most significant advantages is the ability to create custom shapes and designs tailored to specific needs.
- Cost-Effectiveness: Compared to other manufacturing methods, vacuum forming is often more economical, especially for small to medium production runs.
- Lightweight: Vacuum-formed products tend to be lighter than their counterparts made from metals or glass, making them easier to handle and transport.
- Durability: Many vacuum-formed plastics are resistant to impacts, UV radiation, and chemicals, enhancing their longevity in various applications.
Choosing Vacuum Form Plastic Sheet Suppliers
When selecting Vacuum Forming Plastic Sheet Suppliers, consider the following factors:
1. Quality Assurance
Ensure that the supplier adheres to industry standards and offers high-quality materials. Look for certifications that validate the quality of their products.
2. Customization Options
Choose suppliers that offer a range of customization options. This includes various material types, thicknesses, and the ability to produce custom shapes.
3. Experience and Expertise
Select suppliers with a proven track record in the industry. Experienced suppliers like Pulkit Plastic Products can provide valuable insights and guidance throughout the process.
4. Cost and Lead Time
Compare prices from multiple suppliers to ensure competitive pricing. Additionally, consider their lead times for production and delivery, especially if you have tight deadlines.
5. Customer Support
A reliable supplier should offer excellent customer service, including support for inquiries, troubleshooting, and after-sales service.
Conclusion
Vacuum Form Plastic Sheets offer an incredible range of applications across multiple industries, from packaging to automotive and medical fields. Their versatility, cost-effectiveness, and durability make them an excellent choice for businesses looking to innovate and enhance their product offerings. By selecting reputable vacuum forming plastic sheet suppliers, such as Pulkit Plastic Products, you can ensure that you receive high-quality materials tailored to your specific needs. As the demand for innovative and efficient manufacturing processes continues to grow, vacuum forming will undoubtedly remain a vital component of modern production techniques.
FAQs
1. What is the difference between vacuum forming and thermoforming?
Both processes involve heating plastic sheets, but vacuum forming specifically uses a vacuum to shape the plastic over a mold, while thermoforming may not always involve a vacuum and can use pressure instead.
2. What types of plastics can be used for vacuum forming?
Common plastics used in vacuum forming include acrylic, polycarbonate, polystyrene, and ABS. The choice of material often depends on the application and desired characteristics.
3. How thick can vacuum form plastic sheets be?
The thickness of vacuum form plastic sheets typically ranges from 0.020 inches to 0.250 inches, depending on the material and specific requirements of the application.
4. Are vacuum form plastic sheets environmentally friendly?
Many vacuum-formed plastics can be recycled, but it depends on the material used. Always check with suppliers regarding recycling options and environmental impact.
5. Where can I purchase vacuum form plastic sheets?
Vacuum form plastic sheets can be purchased from specialized suppliers and manufacturers. Companies like Pulkit Plastic Products offer a range of options suitable for various applications.
6. Can vacuum-formed products be painted or decorated?
Yes, vacuum-formed products can be painted or decorated. However, surface preparation may be necessary to ensure proper adhesion of paints and coatings.
- Art
- Causes
- Crafts
- Dance
- Drinks
- Film
- Fitness
- Food
- Juegos
- Gardening
- Health
- Inicio
- Literature
- Music
- Networking
- Otro
- Party
- Religion
- Shopping
- Sports
- Theater
- Wellness
