What Are the Best Cutting Parameters for CNC Machining Titanium Alloys?
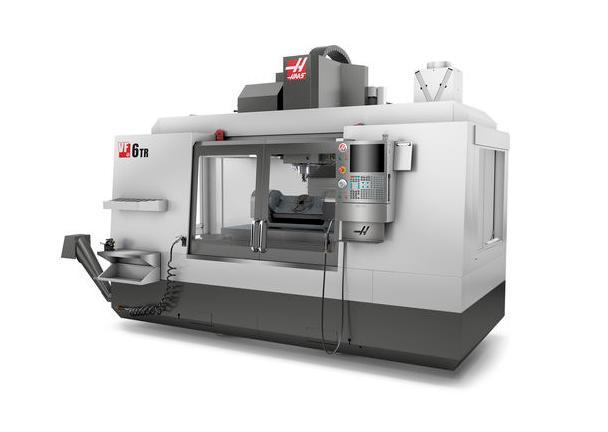
The optimal cutting parameters for CNC machining titanium alloys can vary depending on factors such as the specific alloy, workpiece geometry, desired surface finish, and tool life requirements. However, some general guidelines include:
· Cutting speed: A moderate cutting speed is often recommended to balance productivity and tool life. Higher cutting speeds can increase productivity but may also lead to increased heat generation and tool wear.
· Feed rate: A lower feed rate can help to reduce cutting forces and heat generation, but it may also result in longer machining times. The appropriate feed rate depends on the desired surface finish and tool wear characteristics.
· Depth of cut: Taking smaller depth of cuts can help to manage heat generation and reduce tool wear. However, larger depth of cuts can increase productivity. The optimal depth of cut should be selected based on the workpiece geometry and the desired material removal rate.
· Coolant flow rate: A sufficient coolant flow rate is essential for effective heat removal and chip evacuation. The coolant flow rate should be adjusted based on the cutting conditions and the specific coolant being used.
It is important to experiment with different cutting parameters to determine the optimal settings for a particular machining application. Monitoring tool wear, workpiece quality, and overall process efficiency can help to identify the best combination of cutting parameters.
- Art
- Causes
- Crafts
- Dance
- Drinks
- Film
- Fitness
- Food
- Игры
- Gardening
- Health
- Главная
- Literature
- Music
- Networking
- Другое
- Party
- Religion
- Shopping
- Sports
- Theater
- Wellness
