Evaluating the Cooling Requirements of Electric Grease Bucket Pumps Post-Long-Term Use
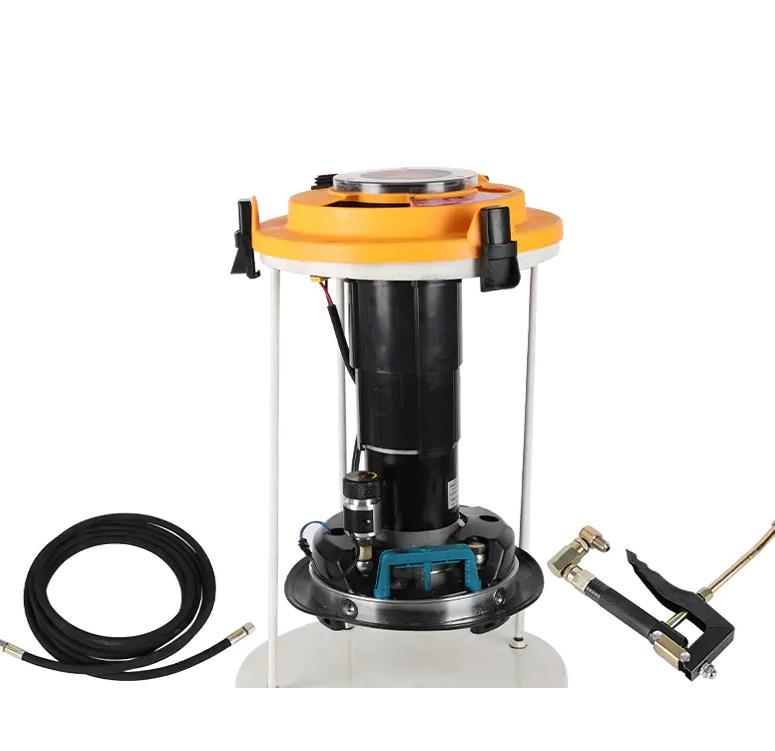
The Electric Grease Bucket Pump, a critical component in many industrial and automotive maintenance processes, is designed to handle the transfer of viscous lubricants with precision. However, the question of whether these pumps require cooling after extended periods of operation is a significant one, as it directly impacts the longevity, efficiency, and safety of the equipment. This article aims to explore the thermal dynamics of Electric Grease Bucket Pumps and the implications of their operation on the need for cooling.
The operation of an Electric Grease Bucket Pump involves the mechanical movement of grease, which is inherently a viscous substance. This movement generates heat due to the friction between the moving parts and the resistance offered by the grease itself. Over time, this heat can accumulate, potentially leading to an increase in the temperature of the pump's components. The question then becomes whether this temperature rise is significant enough to necessitate cooling measures to maintain the pump's optimal performance and prevent damage.
One of the primary factors influencing the need for cooling in an Electric Grease Bucket Pump is the material composition of its components. Pumps with components made from materials that are more resistant to heat and wear are less likely to require cooling. However, even these materials can be affected by prolonged exposure to high temperatures, which can lead to a decrease in their mechanical properties and an increase in the risk of failure.
Another factor to consider is the design of the Electric Grease Bucket Pump. Some pumps are designed with built-in cooling mechanisms, such as heat sinks or cooling jackets, which can help dissipate heat more effectively. These designs can reduce the need for external cooling systems, but they may still require periodic maintenance to ensure that the cooling channels are clear and functioning properly.
The environment in which the Electric Grease Bucket Pump is used also plays a role in determining the need for cooling. In hot and humid conditions, the pump may generate more heat and require more frequent cooling to prevent overheating. Conversely, in cooler environments, the pump may be able to operate for longer periods without the need for additional cooling.
The frequency and duration of use are also critical factors. An Electric Grease Bucket Pump that is used intermittently may not require cooling as frequently as one that is in constant operation. However, even with intermittent use, it is essential to monitor the temperature of the pump to ensure that it does not exceed safe operating limits.
In conclusion, the need for cooling in an Electric Grease Bucket Pump after extended operation is a complex issue that depends on several factors, including the material composition of the pump, its design, the operating environment, and the frequency and duration of use. It is essential for operators to be aware of these factors and to implement appropriate cooling strategies to ensure the longevity and safety of their Electric Grease Bucket Pumps. Regular maintenance and monitoring of the pump's temperature can help prevent damage and ensure that the pump continues to operate efficiently and effectively.
- Art
- Causes
- Crafts
- Dance
- Drinks
- Film
- Fitness
- Food
- Oyunlar
- Gardening
- Health
- Home
- Literature
- Music
- Networking
- Other
- Party
- Religion
- Shopping
- Sports
- Theater
- Wellness
