The Varied Efficiency of Multi Screw Extruder Across Plastic Material Types
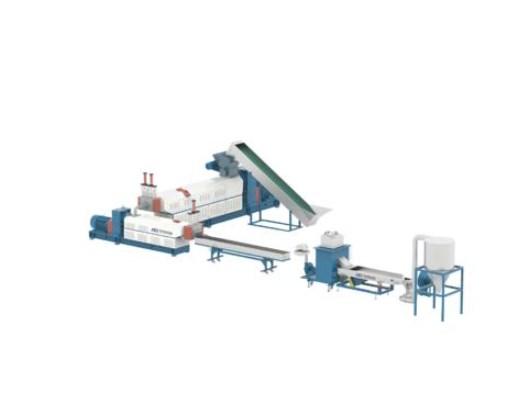
The Multi Screw Extruder, a pivotal piece of equipment in the plastics industry, is renowned for its ability to process a wide array of plastic materials. However, the performance of this machinery can vary significantly depending on the type of plastic being processed. This article delves into the nuances of how Multi Screw Extruders handle different plastics, highlighting the factors that contribute to these performance differences.
The Multi Screw Extruder's design, with its multiple screws rotating in a barrel, allows for a more complex and efficient mixing and melting process compared to single-screw extruders. This design is particularly beneficial when dealing with materials that require high shear or have a wide range of melt viscosities. For instance, when processing polyethylene, a material known for its low viscosity, the Multi Screw Extruder can maintain a consistent output with minimal energy expenditure. The parallel screws work in tandem to ensure uniform melting and mixing, which is crucial for producing high-quality polyethylene products.
In contrast, when the Multi Screw Extruder is tasked with processing polyvinyl chloride (PVC), a material with a higher viscosity, the machine's performance is tested differently. PVC requires higher temperatures and specific screw designs to prevent degradation. The Multi Screw Extruder's ability to adjust temperature profiles and screw configuration allows it to handle PVC effectively, ensuring that the material does not degrade and that the final product maintains its desired properties.
The processing of engineering plastics, such as polyamides (PA) and polycarbonates (PC), presents another set of challenges for the Multi Screw Extruder. These materials are sensitive to heat and can degrade if exposed to high temperatures for extended periods. The Multi Screw Extruder's precise temperature control and efficient heat transfer capabilities are essential in maintaining the integrity of these materials. Additionally, the screws' design must be tailored to the specific rheological properties of each engineering plastic to ensure optimal processing.
When it comes to processing recycled plastics, the Multi Screw Extruder faces yet another set of challenges. Recycled materials often have inconsistent quality and can contain contaminants. The Multi Screw Extruder's robust design and ability to handle a wide range of materials make it well-suited for recycling applications. Its multiple screws can effectively separate and blend the varied components of recycled plastics, resulting in a more uniform output.
The versatility of the Multi Screw Extruder is further demonstrated in its ability to process thermosetting plastics, such as phenolic resins. These materials require precise temperature control and specific processing conditions to prevent premature curing. The Multi Screw Extruder's advanced control systems and customizable screw configurations enable it to meet these demands, ensuring that thermosetting plastics are processed without issues.
In summary, the performance of the Multi Screw Extruder in processing different plastic materials is influenced by a multitude of factors, including the material's viscosity, thermal sensitivity, and the presence of contaminants. The machine's design, with its multiple screws and advanced control systems, allows it to adapt to these varying conditions, making it a versatile and efficient choice for a wide range of plastic processing applications. As the plastics industry continues to evolve, the Multi Screw Extruder remains a critical component in meeting the diverse demands of material processing, showcasing its adaptability and resilience in the face of different plastic materials.
- Art
- Causes
- Crafts
- Dance
- Drinks
- Film
- Fitness
- Food
- Jeux
- Gardening
- Health
- Domicile
- Literature
- Music
- Networking
- Autre
- Party
- Religion
- Shopping
- Sports
- Theater
- Wellness
