The Importance of Quality Control in Electric Power Tools Factories
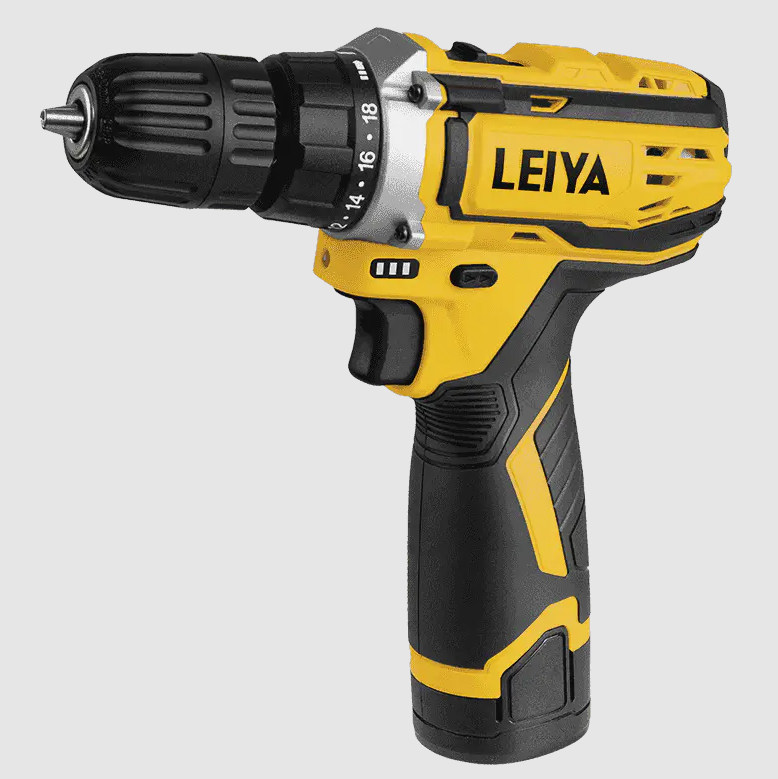
Quality control is one of the most crucial aspects of electric power tools manufacturing. In order to meet the strict standards of safety, durability, and performance, manufacturers must implement a variety of testing and inspection processes throughout production.
The first step in quality control often begins with the selection of materials. Factories use only materials that meet specific safety and performance standards, ensuring that the finished products are capable of withstanding the wear and tear typical in demanding environments.
During production, multiple checks are made to confirm that each component is properly assembled. Visual inspections, measurements, and functional tests are conducted to ensure the tools' safety features, such as electrical insulation and mechanical integrity, meet the necessary regulations.
In addition, automated systems are increasingly used for more accurate and detailed inspections. These systems can check for micro-level defects in the materials or assembly, which might not be visible to the human eye.
Post-production testing is just as important as the assembly line checks. Each tool undergoes functional testing to confirm that it works as expected. This often includes stress testing, where the tools are subjected to conditions they might face in real-world use. Tools that pass these tests are then packaged and prepared for shipment, while those that fail are sent back for repairs or adjustments.
This rigorous approach ensures that only high-quality electric power tools are delivered to customers, maintaining the reputation of manufacturers and ensuring consumer safety.
- Art
- Causes
- Crafts
- Dance
- Drinks
- Film
- Fitness
- Food
- Spellen
- Gardening
- Health
- Home
- Literature
- Music
- Networking
- Other
- Party
- Religion
- Shopping
- Sports
- Theater
- Wellness
