What Are the Key Considerations for CNC Machining Brass and Copper?
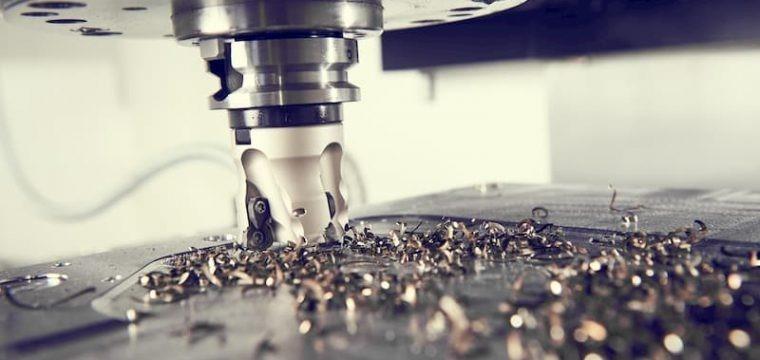
There are some key considerations for CNC machining brass and copper:
Material Selection:
l Brass: Choose the appropriate brass alloy based on the desired properties (e.g., C360 for general machinability, C260 for high corrosion resistance). Consider factors like strength, ductility, and cost.
l Copper: Select the specific copper alloy (e.g., C11000, C12200) based on the application's requirements for electrical or thermal conductivity, work hardening, and machinability.
Machining Parameters:
l Cutting Tools: Use sharp, wear-resistant cutting tools specifically designed for machining brass and copper. Consider tools with appropriate geometries and coatings to minimize heat generation and improve chip evacuation.
l Cutting Speeds and Feeds: Optimize cutting parameters to achieve the desired surface finish, dimensional accuracy, and tool life. Higher cutting speeds and feeds are generally possible with brass and copper due to their good machinability.
l Coolant Selection: Employ a suitable coolant to reduce heat generation, improve chip removal, and extend tool life. Consider using flood or mist coolants based on the specific machining operation.
Workholding: Secure the workpiece firmly to prevent movement during machining. Use appropriate fixtures or clamps to minimize vibration and ensure dimensional accuracy.
Tool Wear Monitoring: Implement a system to monitor tool wear and replace tools promptly to maintain consistent part quality and prevent unexpected failures.
- Art
- Causes
- Crafts
- Dance
- Drinks
- Film
- Fitness
- Food
- Oyunlar
- Gardening
- Health
- Home
- Literature
- Music
- Networking
- Other
- Party
- Religion
- Shopping
- Sports
- Theater
- Wellness
