What Are the Challenges of CNC Machining Titanium? How Can These Challenges Be Overcome?
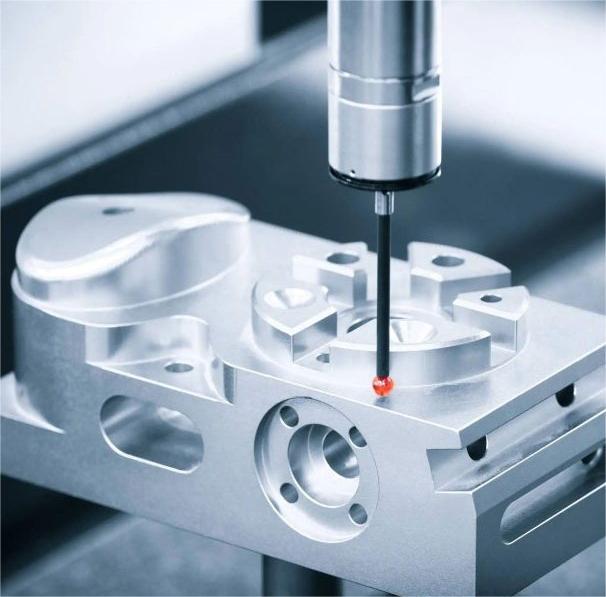
Challenges of CNC Machining Titanium
l Tool Wear: Titanium is a very hard and abrasive material. This can lead to rapid wear and tear of cutting tools, increasing costs and downtime for tool replacement.
l Heat Generation: Titanium has low thermal conductivity, meaning it retains heat easily during machining. This heat buildup can cause tool failure, part distortion, and reduced machining accuracy.
l Work Hardening: As titanium is machined, it tends to become harder, increasing cutting forces and further exacerbating tool wear. This can make it challenging to maintain consistent machining parameters.
l Cost: Specialized tooling, slower machining speeds, and increased tool wear can make CNC machining titanium more expensive than other metals.
Overcoming the Challenges of CNC Machining Titanium
l Specialized Tooling: Utilizing cutting tools specifically designed for machining titanium, such as those made from high-strength ceramics or coated with advanced coatings, can significantly improve tool life and reduce wear.
l Effective Cooling: Implementing high-pressure coolant systems can effectively dissipate heat generated during machining, preventing tool failure and maintaining dimensional accuracy.
l Optimized Cutting Parameters: Adjusting cutting speeds, feed rates, and depths of cut based on the specific titanium alloy and the desired part geometry can minimize heat generation and reduce tool wear.
l Experienced Machinists: Skilled operators with expertise in titanium machining can optimize processes, select appropriate tools, and troubleshoot issues effectively, minimizing downtime and improving overall efficiency.
- Art
- Causes
- Crafts
- Dance
- Drinks
- Film
- Fitness
- Food
- Jeux
- Gardening
- Health
- Domicile
- Literature
- Music
- Networking
- Autre
- Party
- Religion
- Shopping
- Sports
- Theater
- Wellness
