Why Anodize Parts After CNC Machining?
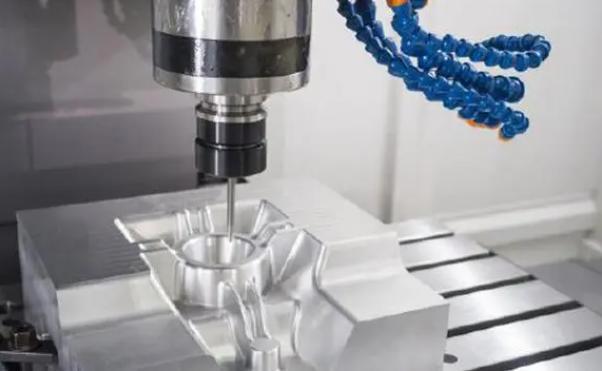
Anodizing offers several significant advantages when applied to CNC machined parts:
Enhanced Corrosion Resistance: Aluminum, while lightweight and versatile, is susceptible to corrosion in certain environments. Anodizing creates a protective oxide layer on the surface, acting as a barrier against moisture, chemicals, and salt. This is crucial for parts exposed to harsh conditions like marine environments, industrial settings, or outdoor applications.
Improved Wear Resistance: The anodized layer significantly increases the surface hardness of the aluminum. This translates to enhanced resistance to abrasion, scratching, and wear and tear. Anodized parts can withstand more rigorous use and maintain their integrity for longer periods.
Enhanced Aesthetic Appeal: Anodizing provides a range of attractive finishes, from clear and natural to vibrant colors. This allows for customization and can improve the visual appeal of the final product. It can also enhance brand identity by incorporating company colors or unique finishes.
Electrical Insulation: The anodized layer provides excellent electrical insulation properties. This is valuable in applications where electrical conductivity needs to be minimized or controlled.
Improved Adhesion: The porous nature of the anodized layer enhances the adhesion of paints, adhesives, and coatings. This ensures a more durable and long-lasting bond between the part and any subsequent finishes.
- Art
- Causes
- Crafts
- Dance
- Drinks
- Film
- Fitness
- Food
- الألعاب
- Gardening
- Health
- الرئيسية
- Literature
- Music
- Networking
- أخرى
- Party
- Religion
- Shopping
- Sports
- Theater
- Wellness
