How Automation Is Revolutionizing Valve and Fittings Manufacturing
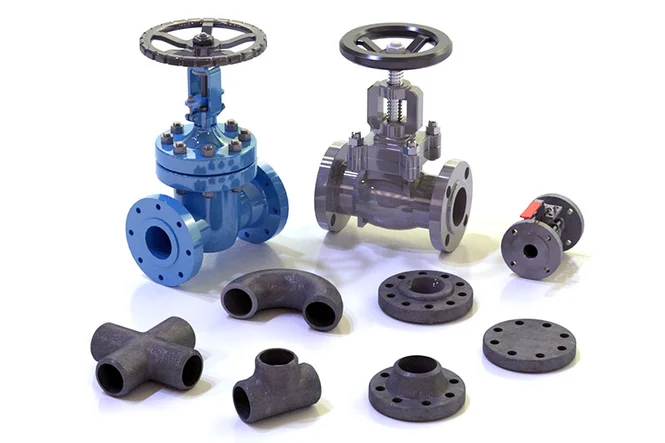
Introduction
In the fast-paced world of industrial manufacturing, automation has emerged as a game-changer. The valve and fittings manufacturing sector, known for its precision and complexity, is undergoing a significant transformation due to automation. Traditional manufacturing processes, which relied heavily on manual labor, are now being replaced by automated systems that enhance efficiency, reduce costs, and improve product quality. This article explores how automation is revolutionizing valve and fittings manufacturing, its benefits, challenges, and the future of the industry.
The Role of Automation in Valve and Fittings Manufacturing
Automation in valve and fittings manufacturing involves the use of advanced machinery, robotics, and computer-controlled systems to streamline production. These systems replace repetitive manual Valve and Fittings Manufacturer tasks, allowing manufacturers to increase productivity and maintain consistent quality. The following are key areas where automation is making a substantial impact:
1. Precision Machining and Fabrication
Modern Computer Numerical Control (CNC) machines have replaced conventional machining methods, ensuring high precision in valve and fittings production. These automated machines can operate with minimal human intervention, reducing errors and material wastage while producing highly accurate components.
2. Robotics in Assembly Lines
Robotic arms and automated assembly lines have enhanced the efficiency of valve and fittings production. These robots handle tasks such as welding, threading, and assembling parts with unmatched accuracy. By reducing human errors, they improve the overall reliability and durability of manufactured products.
3. Quality Control and Inspection
Automation has significantly improved quality control through the use of advanced sensors, vision inspection systems, and artificial intelligence (AI). Automated inspection systems can detect defects in real time, ensuring that only high-quality valves and fittings reach the market. This eliminates the need for manual inspection, which can be time-consuming and prone to errors.
4. Supply Chain and Inventory Management
Automation is also transforming supply chain management in the valve and fittings industry. Automated tracking systems, powered by IoT (Internet of Things) and AI, allow manufacturers to monitor inventory levels, optimize raw material usage, and prevent production delays. This ensures seamless production flow and minimizes downtime.
Benefits of Automation in Valve and Fittings Manufacturing
The adoption of automation offers numerous advantages that enhance efficiency, safety, and cost-effectiveness in valve and fittings production:
1. Increased Productivity
Automated systems operate faster and with greater precision than manual labor, significantly increasing production output. Manufacturers can meet higher demands without compromising quality.
2. Enhanced Quality and Consistency
Automation minimizes human errors and ensures uniformity in production. CNC machines, robotic assembly lines, and AI-driven quality control systems maintain strict adherence to design specifications, resulting in superior products.
3. Cost Savings
Although the initial investment in automation technology can be high, it ultimately leads to cost savings. Reduced labor costs, minimal material wastage, and efficient energy consumption contribute to long-term financial benefits.
4. Improved Workplace Safety
Automation reduces the need for human workers to perform hazardous tasks, such as handling high-temperature materials or working with heavy machinery. This minimizes workplace injuries and enhances overall safety standards.
5. Faster Time-to-Market
With automated production lines, manufacturers can quickly scale up production and meet market demands efficiently. This is particularly beneficial in industries where rapid delivery of components is crucial.
Challenges of Implementing Automation
Despite its numerous advantages, automation in valve and fittings manufacturing also presents certain challenges that need to be addressed:
1. High Initial Investment
Implementing automation requires significant capital investment in advanced machinery, software, and training. Small and medium-sized enterprises (SMEs) may find it difficult to afford these expenses.
2. Workforce Adaptation
The shift from manual to automated processes necessitates workforce training and reskilling. Employees need to be familiar with operating and maintaining automated systems, which requires continuous learning.
3. System Integration and Maintenance
Integrating automated systems with existing manufacturing processes can be complex. Ensuring seamless communication between different systems, such as IoT-enabled devices and AI-driven analytics, requires technical expertise and regular maintenance.
4. Cybersecurity Concerns
As automation relies on interconnected digital systems, it becomes vulnerable to cyber threats. Manufacturers must invest in robust cybersecurity measures to protect sensitive data and maintain operational security.
The Future of Automation in Valve and Fittings Manufacturing
The future of valve and fittings manufacturing is poised for further advancements in automation. Emerging technologies such as artificial intelligence, machine learning, and Industry 4.0 are expected to drive even greater efficiencies and innovation.
1. Smart Factories and Industry 4.0
Industry 4.0 integrates automation with IoT, AI, and big data analytics to create smart factories. These intelligent manufacturing environments enable real-time monitoring, predictive maintenance, and optimized production processes.
2. AI-Powered Predictive Maintenance
Artificial intelligence can analyze vast amounts of data to predict potential equipment failures before they occur. Predictive maintenance helps prevent costly downtime and extends the lifespan of machinery.
3. 3D Printing and Additive Manufacturing
Automation is also facilitating the adoption of 3D printing for rapid prototyping and production of customized valve and fitting components. This reduces lead times and enables manufacturers to meet unique customer requirements efficiently.
4. Collaborative Robotics (Cobots)
Unlike traditional industrial robots, collaborative robots (cobots) work alongside human operators to enhance productivity. These robots are equipped with advanced sensors and AI-driven algorithms that allow them to perform complex tasks while ensuring safety.
Conclusion
Automation is transforming valve and fittings manufacturing by enhancing precision, efficiency, and quality control. While challenges such as high initial costs and workforce adaptation exist, the long-term benefits outweigh the drawbacks. As technological advancements continue, automation will play an increasingly vital role in shaping the future of the industry. Manufacturers who embrace automation today will gain a competitive edge, ensuring sustained growth and innovation in valve and fittings production.
- Art
- Causes
- Crafts
- Dance
- Drinks
- Film
- Fitness
- Food
- الألعاب
- Gardening
- Health
- الرئيسية
- Literature
- Music
- Networking
- أخرى
- Party
- Religion
- Shopping
- Sports
- Theater
- Wellness
