Application of Laser Welding in the Jewelry and Ornament Industry
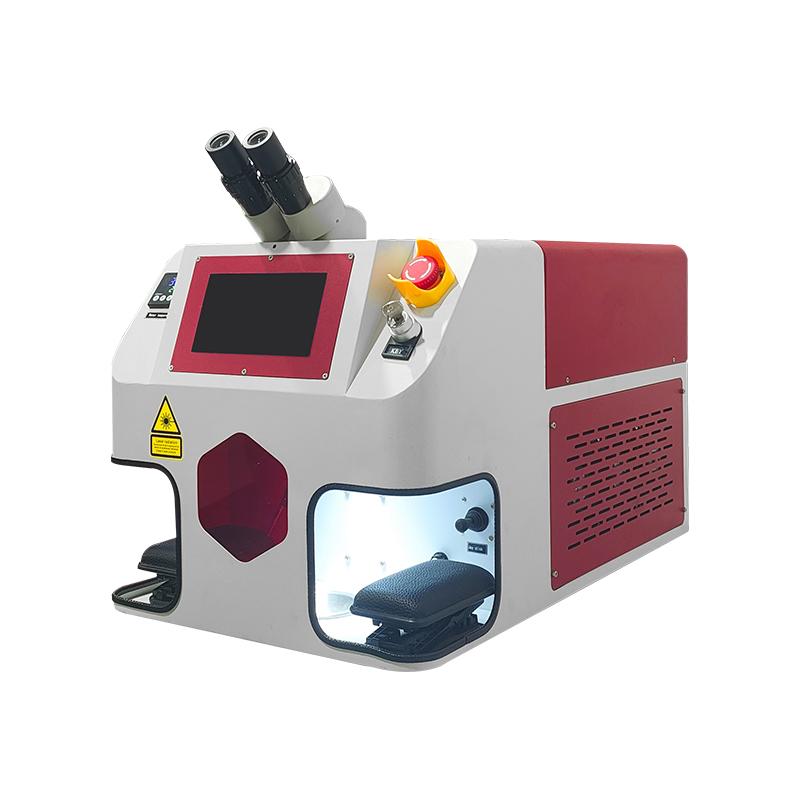
Application of Laser Welding in the Jewelry and Ornament Industry
The application of laser welding machines in the arts and crafts jewelry industry is being utilized and demonstrated, primarily for precision necklaces and other ornaments. Similar to laser marking machines, the application of laser welding in the jewelry industry is continuously developing and becoming more profound. Laser welding involves using high energy to instantly melt and fuse materials together.
The principle of a jewelry laser welding machine is that the surface of the metal undergoes a series of changes under laser irradiation. Its surface is heated by the laser and rapidly conducts heat inwards. When the laser power density reaches a certain level, the surface will melt, and a portion will instantly vaporize at higher laser power densities, forming a molten pool on the workpiece surface. During the welding process, the workpiece moves relative to the laser, causing the molten metal to accelerate along a certain angle. The heat transfer of the liquid metal rapidly decreases the temperature, and the liquid metal forms a weld seam.
Jewelry laser welding machines are mainly used for filling holes, spot welding pinholes, and repairing gold and silver jewelry. Utilizing laser deposition welding, a high-heat energy and concentrated point welding technology, surface heat diffuses internally through conduction. By controlling parameters such as laser pulse width, energy, peak power, and repetition frequency, the workpiece is melted to form a specific molten pool. Due to its unique advantages, it has been successfully applied in the processing of gold and silver jewelry and the welding of micro and small parts.
Laser welding has the characteristics of high welding strength and speed, and a low reject rate, and is widely used in the jewelry manufacturing industry. Compared with traditional welding techniques, it has the following advantages:
1. Fast speed, high strength, small deformation, and no need for shaping and cleaning after welding.
2. Suitable for welding precision workpieces, ensuring processing quality.
3. High assembly accuracy, which helps in developing new processes.
4. Good consistency and stability.
5. Can simplify workpiece repair work.
6. Environmentally friendly and pollution-free.
7. Saves processing metal materials.
- Art
- Causes
- Crafts
- Dance
- Drinks
- Film
- Fitness
- Food
- Spellen
- Gardening
- Health
- Home
- Literature
- Music
- Networking
- Other
- Party
- Religion
- Shopping
- Sports
- Theater
- Wellness
