How Bottle Blowing Machines Boost Production Efficiency?
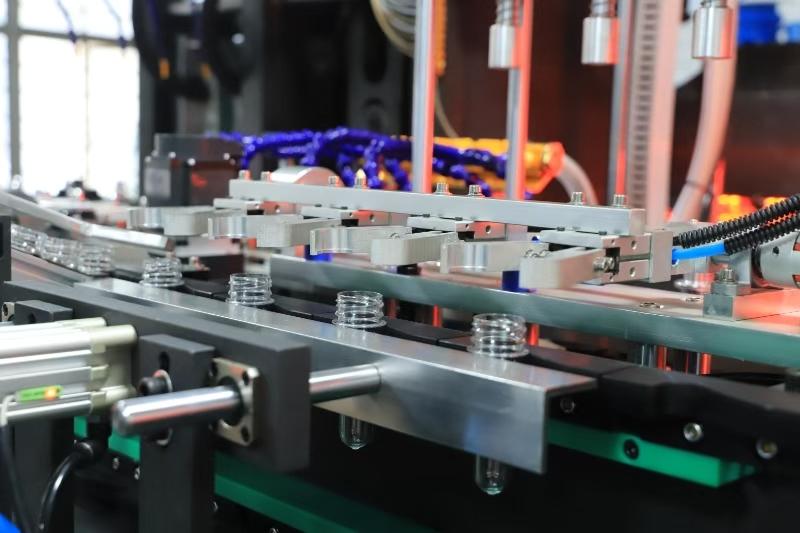
In the modern world of manufacturing, the bottle blowing machine plays a crucial role in the production of plastic bottles. These machines are designed to transform preforms (small, molded pieces of plastic) into full-sized bottles, which are used across various industries such as food and beverage, cosmetics, and pharmaceuticals. The process is highly efficient, automated, and offers several advantages that contribute to the overall productivity and quality of the production line.
The operation of a bottle blowing machine typically involves three main stages: heating, blowing, and cooling. Initially, the preform is inserted into the machine, where it is heated to the right temperature, making it soft and malleable. The machine then uses air pressure to expand the heated preform into a mold, taking the shape of the desired bottle. Finally, the newly formed bottle is cooled before being ejected from the machine.
This process, known as blow molding, can be performed in different ways, including extrusion blow molding, injection blow molding, and stretch blow molding, depending on the material used and the type of bottle being produced. Each method has its specific applications and advantages, allowing manufacturers to choose the most suitable one for their needs.
One of the major advantages of a bottle blowing machine is its ability to produce bottles at high speed. These machines are capable of running continuously, which significantly reduces the time needed to produce large volumes of bottles. This efficiency is particularly important in industries that require quick turnaround times to meet market demand, such as the beverage industry.
By automating the process, a bottle blowing machine reduces the need for manual labor, leading to lower production costs. Furthermore, the high-speed nature of the machine allows manufacturers to produce more bottles in a shorter period, contributing to higher overall productivity. Over time, the initial investment in such equipment can result in substantial cost savings.
Another important feature of bottle blowing machines is their flexibility. Manufacturers can adjust the machine settings to produce bottles of various shapes, sizes, and designs. This versatility is particularly useful when dealing with different products, as it allows companies to meet specific packaging requirements and cater to a variety of customer preferences.
The automation of the bottle-blowing process ensures a higher degree of consistency compared to manual methods. Every bottle produced on the machine will have the same size, shape, and wall thickness, which is important for ensuring that the product meets industry standards and customer expectations. Consistent packaging is particularly vital in markets where the appearance of the product is a key selling point.
In recent years, there has been a growing emphasis on sustainability in manufacturing. Modern bottle blowing machines are designed with energy efficiency in mind, using advanced technologies that reduce power consumption during the production process. Additionally, the machines can be equipped with recycling systems to reuse excess plastic material, minimizing waste and promoting environmental responsibility.
The bottle blowing machine is a cornerstone in the production of plastic containers. Its ability to increase efficiency, reduce costs, offer customization options, and ensure consistency in production makes it an invaluable tool for manufacturers across various industries. As technology continues to advance, these machines are likely to become even more efficient, adaptable, and sustainable, further enhancing their role in modern manufacturing.
- Art
- Causes
- Crafts
- Dance
- Drinks
- Film
- Fitness
- Food
- Игры
- Gardening
- Health
- Главная
- Literature
- Music
- Networking
- Другое
- Party
- Religion
- Shopping
- Sports
- Theater
- Wellness
