The Production Process of Aluminum Rolls and Coils
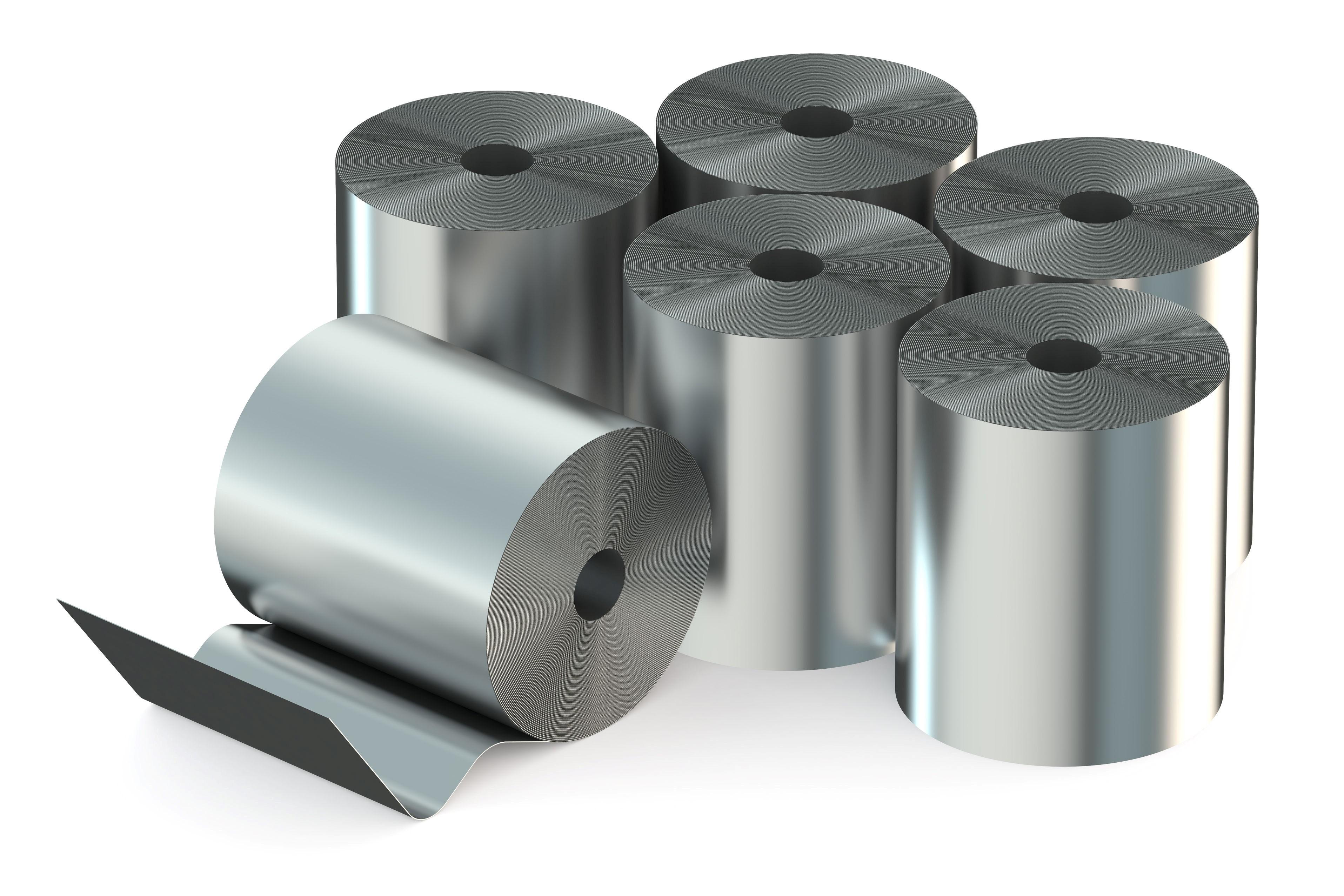
Smelting is the process that is used in extractive metallurgy to create metal from its ore. During the smelting process, heat and a chemical reduction agent are used to break down the ore. This allows for the removal of other components, such as gasses or slag (the stonelike waste material removed from a metal during smelting), and the retention of only the metal itself. In many cases, a carbon-based substance such as coal, coke, or charcoal is used as the reducing agent. In an alumina refinery, the Bayer process is used to extract alumina from the bauxite ore in order to produce pure alumina. Below, an explanation is given for both the Hall-Heroult process as well as the Bayer process. The Bayer process involves dissolving the constituent parts of the particle in order to remove the alumina, which is then refined further through filtration. The smelter will toss out the remaining components after anodized aluminum coil has succeeded in separating the alumina from the bauxite. The particular extraction method will be determined by the type of aluminum component being retrieved. The mineral gibbsite is an aluminum hydroxide and belongs to the oxides and hydroxides group. Its structural formula is Al(OH), and its name comes from the chemical formula.
By dissolving alumina in molten synthetic cryolite, the Hall-Heroult process is able to reduce the melting point for electrolysis.
Synthetic cryolite is a white, crystalline powder that is produced by combining hydrofluoric acid, sodium carbonate, and aluminum. In the electrolytic production of aluminum, synthetic cryolite is used in a state of flux the vast majority of the time. Cryolite is advantageous in that it can transmit electricity, it has a lower density than aluminum, and it makes it easy to dissolve alumina, which is a compound that contains aluminum.
Electrolysis is used on a large scale in the production of aluminum, and aluminum smelters require a significant amount of energy in order to function effectively.
The price of aluminum coils goes up whenever there is either an increase in the total amount of power required to refine aluminum to a higher grade or in the overall cost of power. In addition, the aluminum that has been dissolved will separate out and be collected in a separate location. Additionally, this method necessitates a significant quantity of energy, which in turn has an effect on the prices of aluminum on the market. The metal stock is then put through one or more sets of rolls, depending on the number of sets being used. Processing the sheet at a temperature of 1700 degrees Fahrenheit results in the creation of an aluminum coil.
Using this method, it is possible to create shapes with the appropriate geometrical parameters and material characteristics while maintaining the same volume of metal throughout the process. Plates and sheets, both semi-finished and finished products, can't be made without these operations, which are absolutely necessary.
The third step is the cold rolling.
The cold rolling of metal strips is a specialized technique that is only used in the metalworking industry. The metal's yield strength and hardness are increased as a result of being squeezed and compressed.
In order to produce strips and sheets of metal with the desired final gauge, a number of different industries utilize a metal treatment procedure known as cold rolling. In order to make the aluminum more workable, the rolls are heated on a regular basis, and lubricant is applied to the rolls in order to prevent the aluminum strip from sticking to the rolls. Alterations to the rolls' movement and heat can be made in order to achieve optimal performance. In the aluminum industry, a strip of aluminum that has already been through hot rolling and various other processes, such as cleaning and treating, is cooled to room temperature before being placed into a cold mill rolling line. This treatment makes the anodized aluminum coil tough enough to withstand cold rolling, and the cleaning process involves rinsing the aluminum with detergent. The lattice planes of the metal are disrupted and off-set throughout the process, which ultimately results in a product that is both more difficult and more robust. Because the thickness of the aluminum is reduced while it is being crushed and pushed through rollers in the process of cold rolling, this technique is one of the most common and widely used methods for strengthening aluminum.
Annealing is the fourth step.
The primary goal of the heat treatment known as the annealing process is to make the material being worked on more malleable and less rigid. This change in hardness and flexibility is brought on by a reduction in the number of dislocations found in the crystal structure of the material that is being annealed.
The annealing process effectively resets the crystalline grain structure, which in turn restores the slip planes and enables the part to be further shaped without requiring an excessive amount of force. To work-harden an aluminum alloy, it is necessary to heat the material to a specific temperature that falls between 570 and 770 degrees Fahrenheit for a specific amount of time, which can range anywhere from about thirty minutes to three hours. Annealing is also a viable treatment option for aluminum alloys, including those that cannot be heat-treated.
Annealing improves the ability of a material to be shaped into a desired shape. Annealing contributes to the elimination of this risk. It's possible that an extremely brittle material could cause an excessive amount of tool wear. The hardness of a material can be reduced using annealing, which in turn can reduce the amount of tool wear. The annealing process releases any tensions that may still be present.
- Art
- Causes
- Crafts
- Dance
- Drinks
- Film
- Fitness
- Food
- Jocuri
- Gardening
- Health
- Home
- Literature
- Music
- Networking
- Alte
- Party
- Religion
- Shopping
- Sports
- Theater
- Wellness
